01
CGSF Servo Ultrasonic Plastic Welding Machine
Brief Description (Core Features)
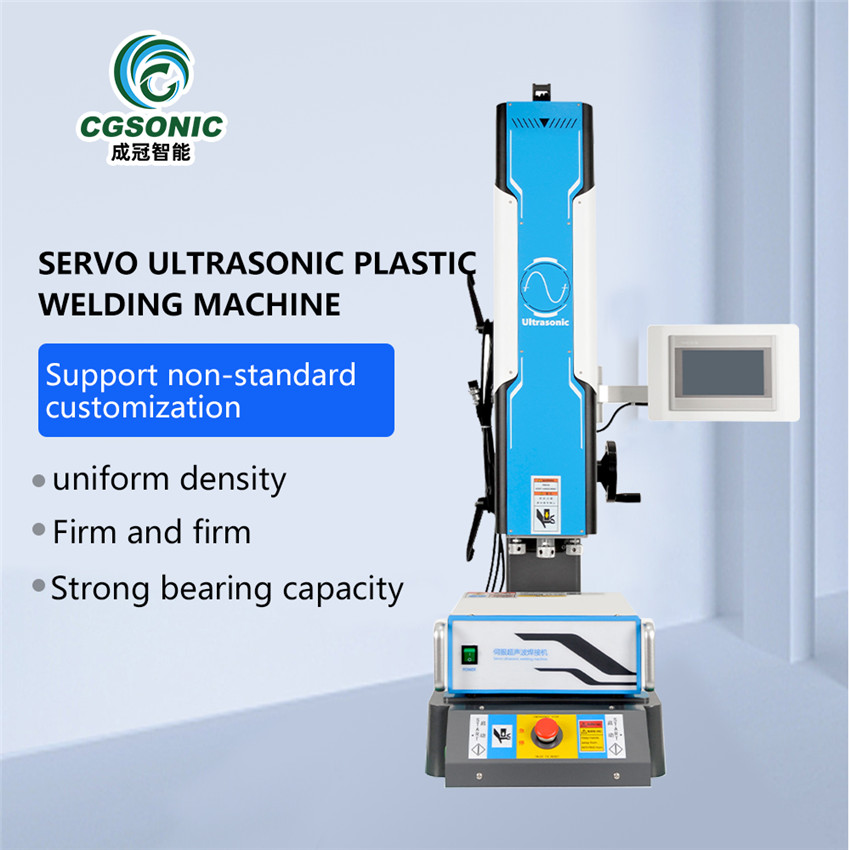
High Efficiency: Fast welding speed and short cycles significantly boost productivity.
Strong Adaptability: Welds plastic parts of different shapes and sizes by simply replacing welding heads or adjusting parameters.
Excellent Welding Quality: Produces aesthetically pleasing, strong, and sealed joints with no visible marks or internal damage.
Low Noise and Pollution: Quieter operation than traditional methods, with no harmful emissions, making it eco-friendly.
Durable Equipment: High-quality key components and a reliable servo system reduce maintenance costs and extend lifespan.
Working Principle
The servo ultrasonic plastic welding machine uses a servo system to precisely control the welding head’s position and pressure. The ultrasonic generator produces high-frequency electrical signals, which are converted into mechanical vibrations by the transducer. These vibrations are amplified by the horn and transmitted to the welding head. The head applies ultrasonic energy to the plastic workpiece, causing molecular friction and localized heating. The plastic melts and fuses under pressure, forming a strong bond upon cooling.
Product Introduction
The servo ultrasonic welding machine integrates ultrasonic technology with servo control for advanced performance. The ultrasonic generator produces high-frequency signals, converted into vibrations by the transducer, while the servo system precisely regulates parameters. With accurate frequency, amplitude, and phase control, ultrasonic energy is applied stably and precisely to the workpiece.
Key advantages include:
High precision: Ideal for micro-component welding.
Stable performance: Reduces defect rates.
Flexibility: Adjustable parameters for diverse applications.
This machine is widely used in:
Electronics: Chip packaging, precision component welding.
Medical Devices: Catheters, sensors, ensuring sterility and sealing.
Automotive: Interior and engine parts, meeting high-strength demands.
Application Fields
Electronics Manufacturing: Welds micro-components in phones, computers, etc., ensuring precision without damaging nearby parts.
Medical Devices: Produces syringes, IV tubes, and sensors, guaranteeing sealing and sterility.
Automotive Industry: Welds interior and engine components, combining strength with weight reduction.
Packaging: Seals plastic containers and films for food, pharmaceuticals, and cosmetics, ensuring airtightness for high-speed production.
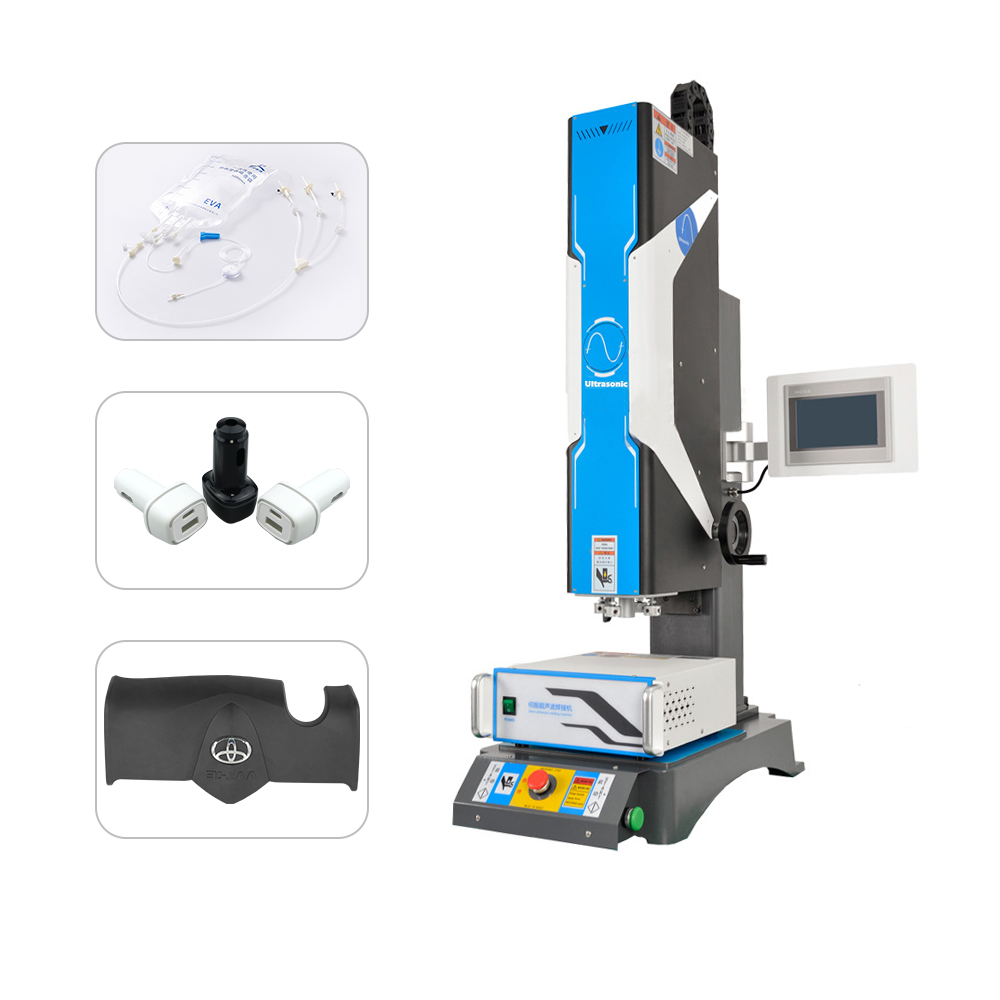
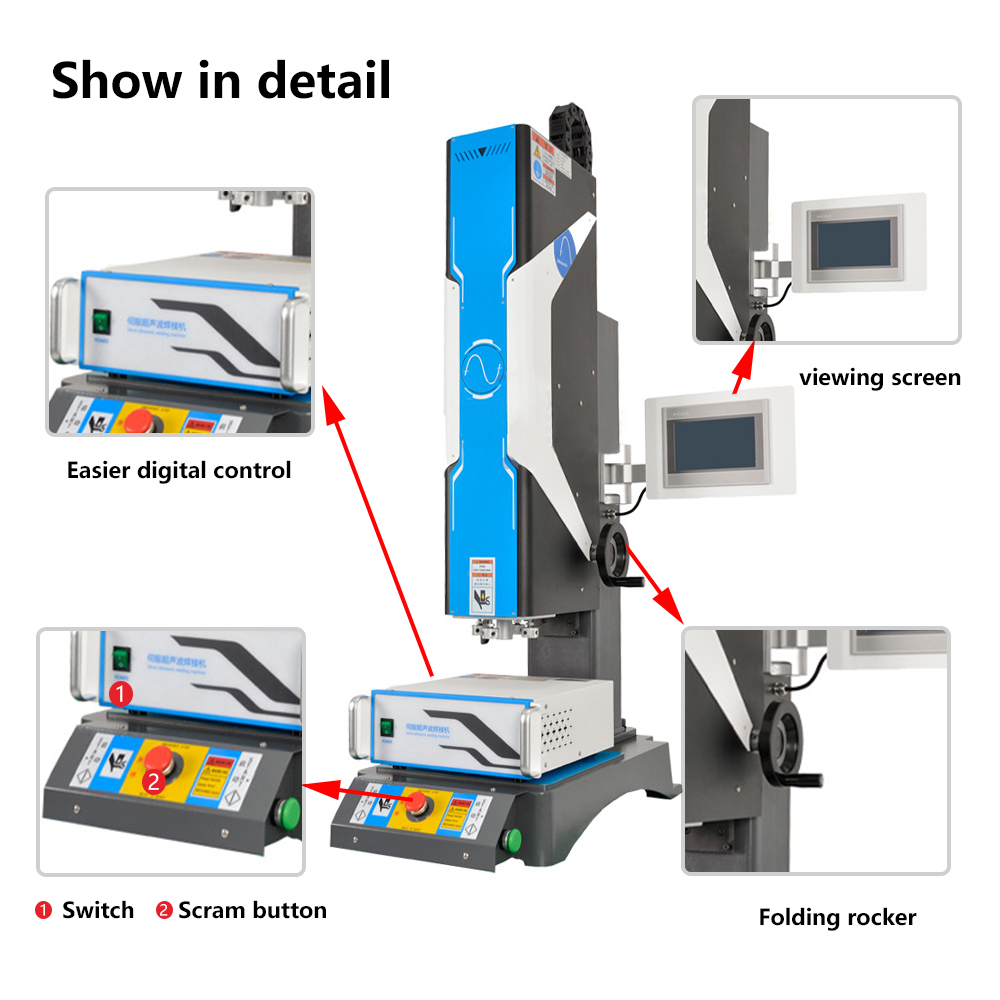
Product Parameters
Parameter |
Specification |
Model |
CGSF |
Frequency |
15KHz/20KHz |
Power |
2000W |
Input Voltage |
AC220V |
Max Bearing Pressure |
300KG |
Servo Stroke |
95mm |
Horn Cooling |
Air Cooling |
Trigger Modes |
Position, Pressure |
Welding Modes |
Distance, Position |
Quality Control |
√ |
Horn Recipe Storage |
√ |
Welding History |
√ |
Anti-Pressure Function |
√ |
Equipment Dimensions |
700×900×1750mm |
Structural Diagram
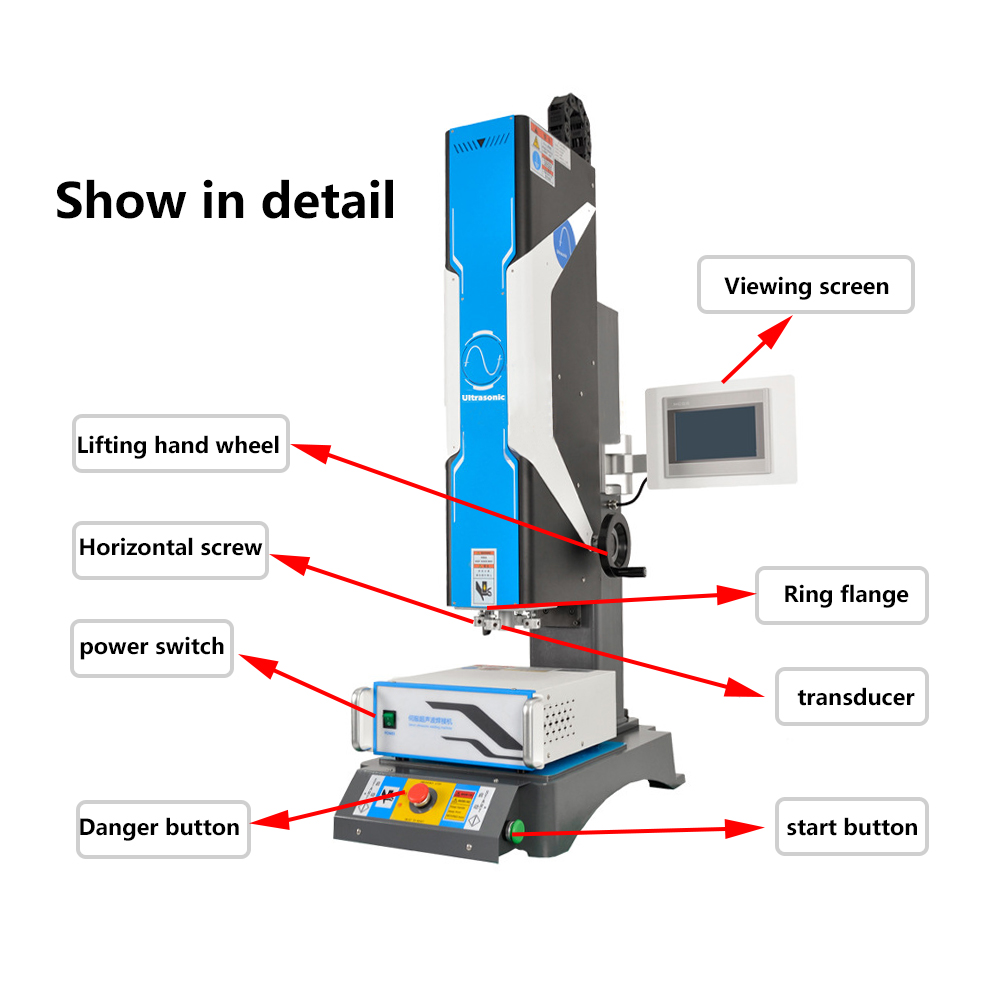
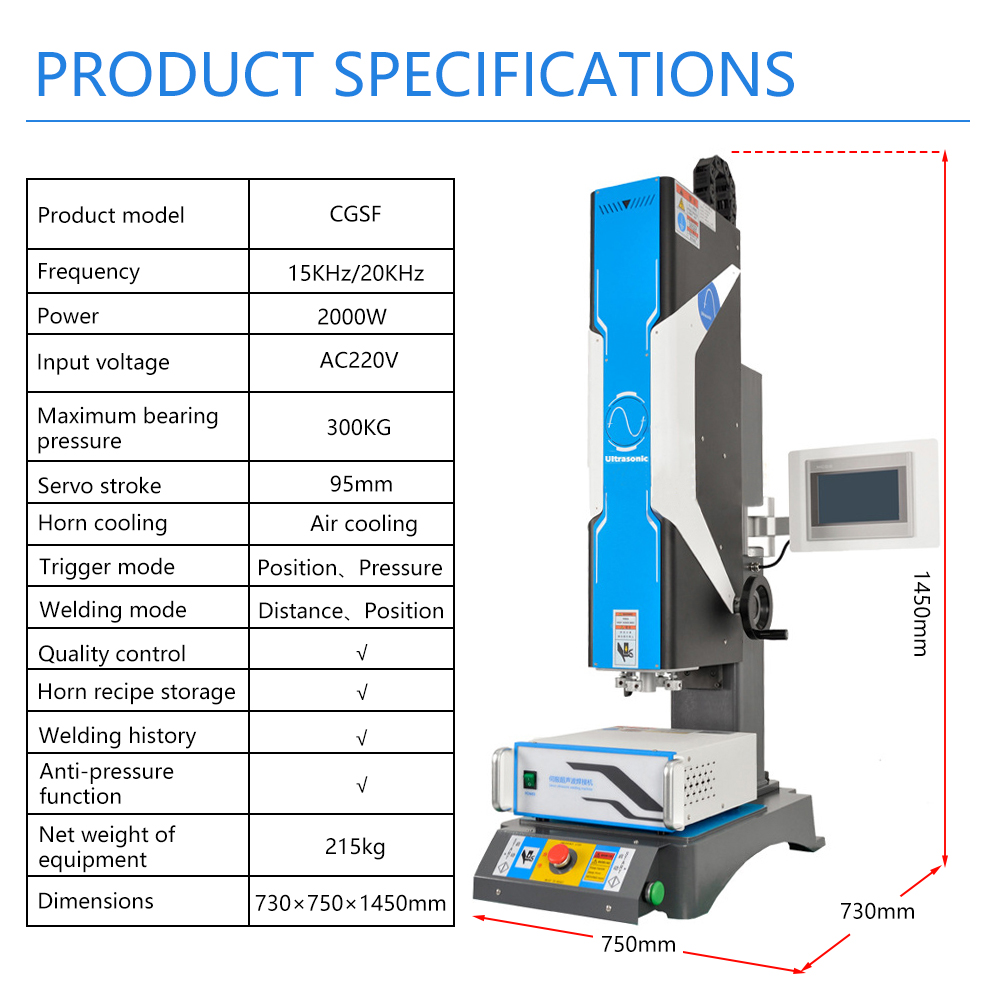
Maintenance Guide
1. Daily Cleaning: Remove plastic debris and oil from the machine, welding head, and worktable after use.
2. Weekly Inspections: Check connections of the generator, transducer, and servo motor; inspect cables for damage.
3. Welding Head Care: Replace worn heads; clean before/after use to prevent contamination.
4. Lubrication: Lubricate rails and lead screws periodically to ensure smooth motion.
5. Cooling System: Ensure fans or water-cooling systems function properly to prevent overheating.
6. Electrical System: Clean control cabinet dust; replace frayed or aged wiring.
7. Storage: Disconnect power and protect key components from dust/humidity during long-term inactivity.
After-Sales Service
Our warranty is 1 years, and if you have any other problems about it, we'll provide you online technical support to help you.