01
Ultrasonic handheld spot welding system
Working Principle
By using an ultrasonic generator to convert 50/60Hz current into high-frequency alternating current, the electrical energy is input into an ultrasonic transducer to generate mechanical motion of the same frequency. The mechanical motion is transmitted to the ultrasonic welding head through an amplitude modulator device, and the welding head transfers the received vibration energy to the joint of the workpiece to be welded. In this area, the energy is converted into heat energy through friction, melting the plastic. After the vibration stops, the brief pressure maintained on the workpiece causes the two welded parts to solidify into one through molecular linkage.
Product Introduction
It mainly consists of ultrasonic transducers, welding heads, shells (direct grip or pistol style), and ultrasonic generators. Compact in size, easy to operate, and able to replace welding heads according to product rivet size and welding requirements. Suitable for welding, riveting and other processes of thermoplastic materials in various industries such as plastic hardware, electronic appliances, automotive parts, etc., it has the advantages of excellent welding quality, high efficiency, energy conservation and environmental protection.
application area
Plastic hardware industry: used for riveting, spot welding, embossing, folder positioning and other processes of plastic parts.
Electronic and electrical industry: plastic casings for weldable electronic components, fixing of wiring harnesses, etc.
Automotive parts industry: such as welding of automotive door panels and interiors, assembly of automotive plastic parts, etc.
Clothing packaging industry: able to weld and fix the lace and accessories of clothing, as well as seal the packaging with plastic film.
Textile industry: used for welding, edge pressing, splicing, etc. of fabrics, avoiding the pinhole problem caused by traditional stitching methods.
Environmental protection industry: such as the production of eco-friendly bags, welding of plastic trash cans, etc.
Medical device industry: It can be used for welding and assembling plastic components of medical devices, requiring high welding accuracy and no pollution.
Toy industry: Assembly and welding of plastic toys to ensure their firmness and safety.
Communication equipment industry: Welding of plastic casings and components in communication equipment.
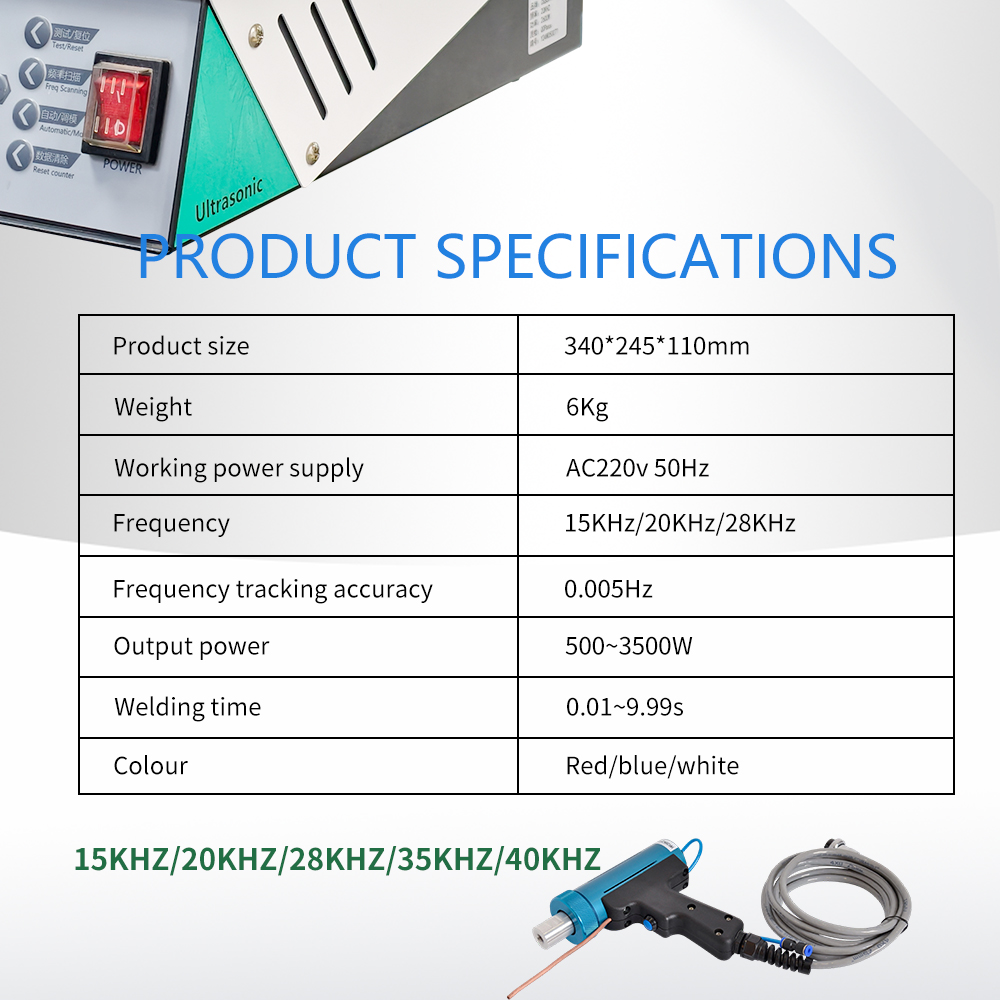

Detail Display
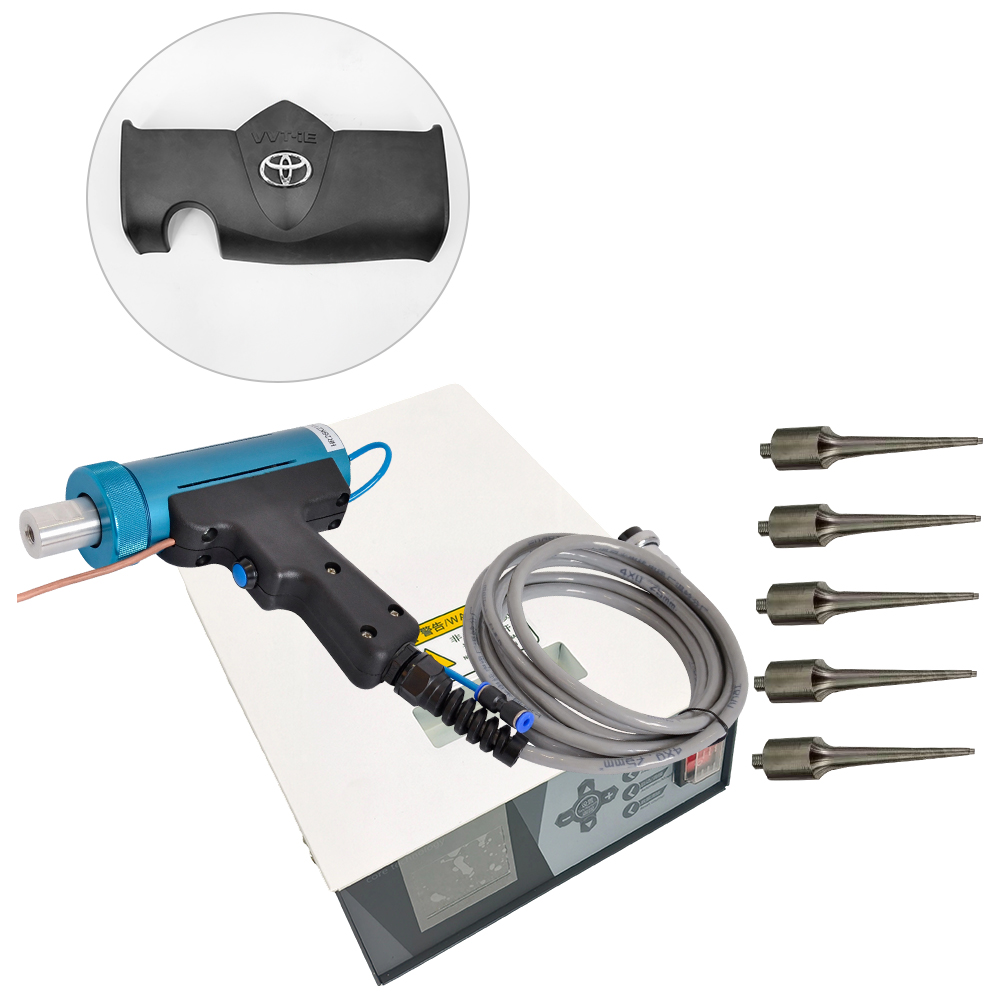
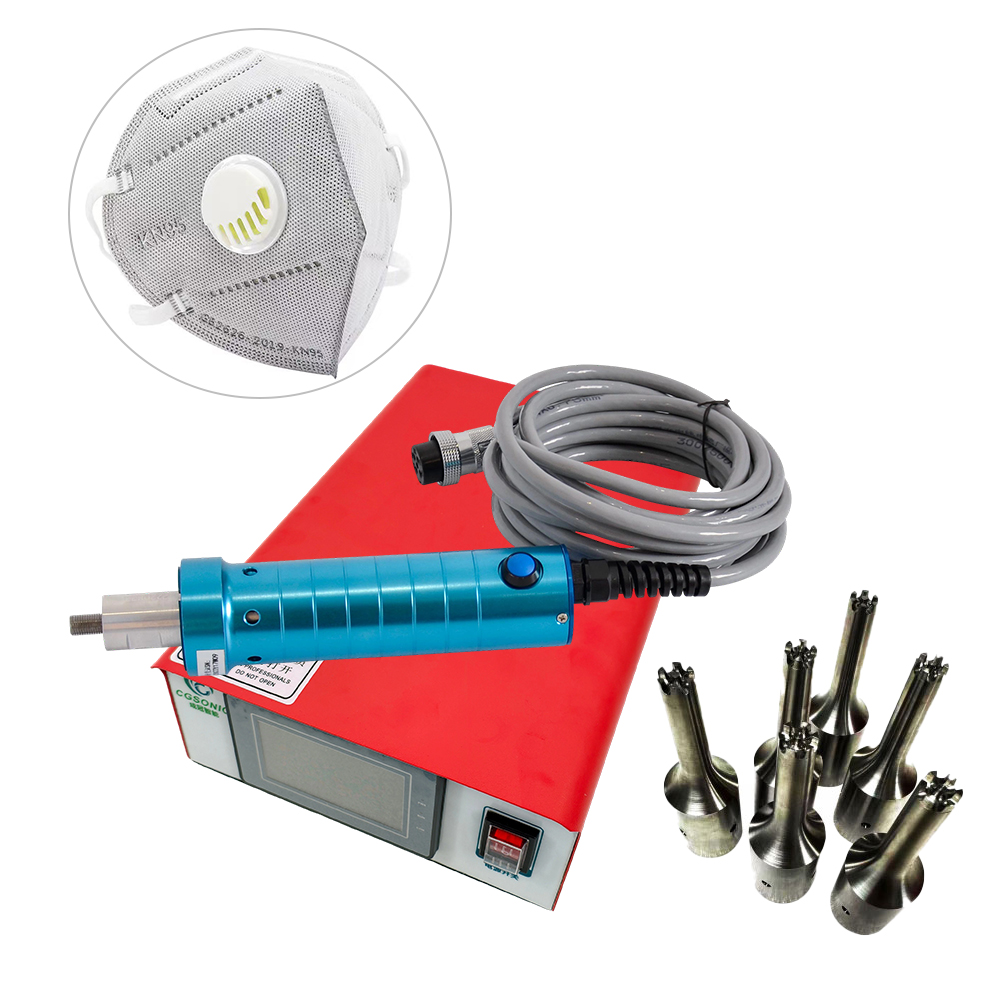
Mold customization
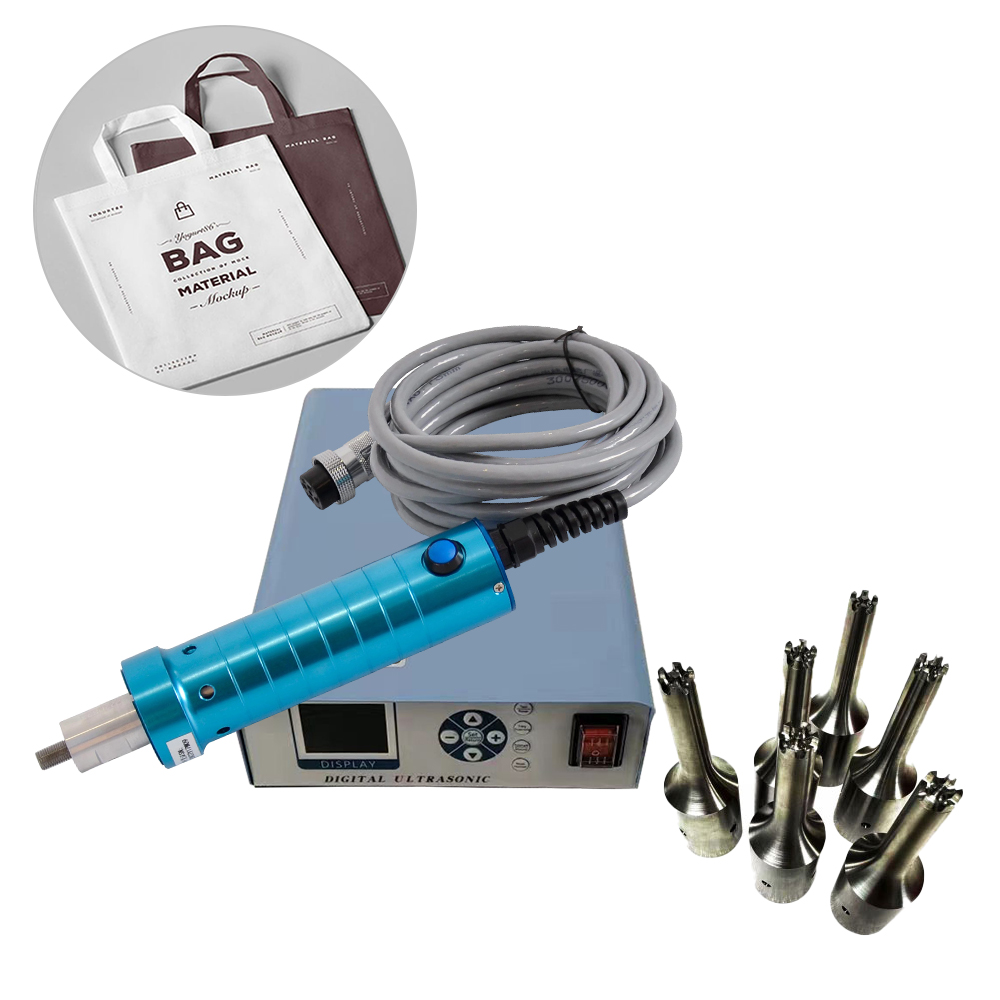
Operating Frequency |
20KHz/28KHz/35KHz/40KHz |
output power |
500~3500W |
Input Voltage |
AC220v 50Hz |
amplitude adjustment |
1%~100% |
weld time |
0.01~9.99s |
Machine maintenance and upkeep
Appearance and overall structure: After each use, wipe the gun body with a clean soft cloth to remove dust, stains, and welding residue. Regularly inspect the gun body for cracks and damage, especially the grip, to ensure safe use. Check the connection parts, such as the connection between the gun head and the gun body, to ensure that they are firm and not loose.
Electrical system: Check whether the power cord is damaged or aged to avoid the risk of leakage; Regularly clean the dust on the electrical components inside the welding gun to ensure good heat dissipation and prevent damage due to overheating. At the same time, check if the control switch is working properly, and if there are any issues such as poor contact, repair or replace it in a timely manner.
Ultrasonic generator: Ensure that the working environment of the generator is dry and avoid moisture. Regularly check the parameter settings of the generator to ensure stable output power and frequency. If any abnormalities are found, adjust or contact professional personnel for maintenance in a timely manner.
Welding head: After each use, clean the welding residue on the welding head in a timely manner to prevent it from affecting the next welding effect. Regularly check the wear of the welding head. If the wear is severe, it needs to be replaced in a timely manner to ensure welding quality.
Regular testing: Conduct performance tests on the handheld welding gun at regular intervals, such as testing welding strength and checking if ultrasonic output is normal, to ensure that the equipment is in optimal working condition.
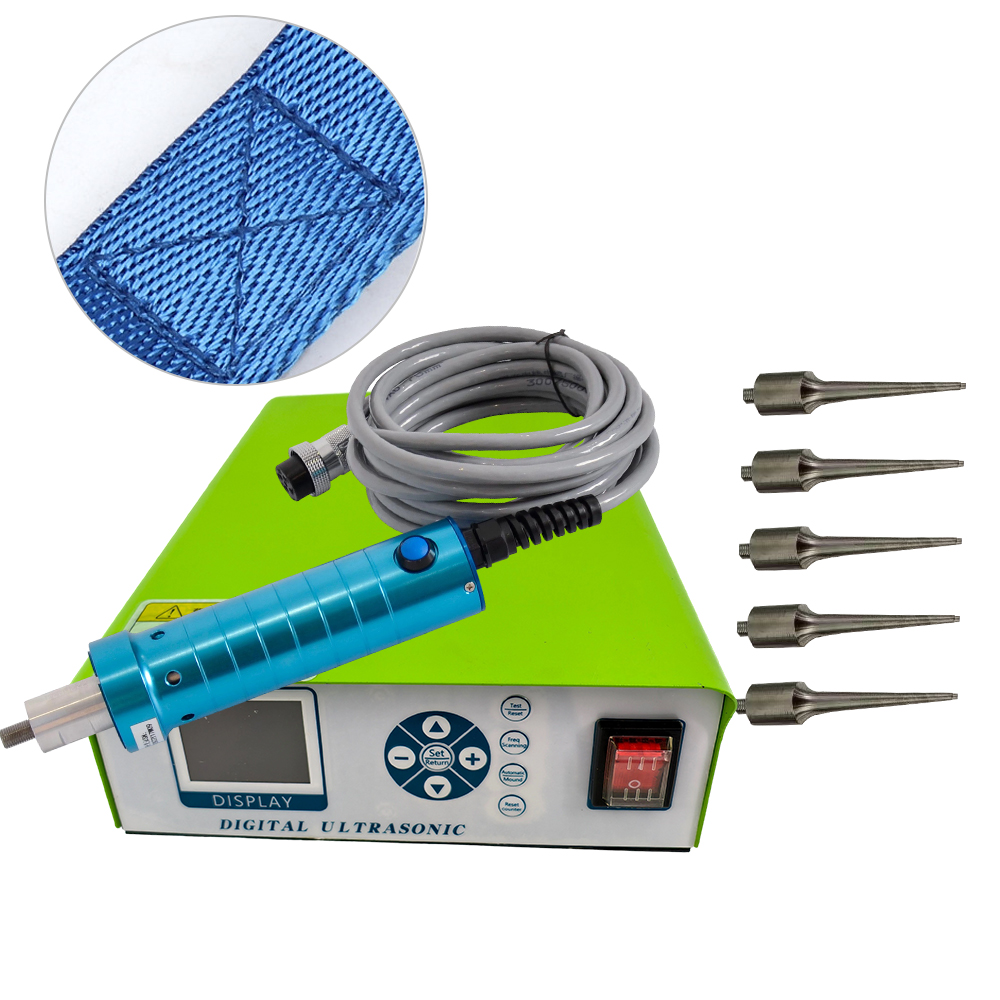
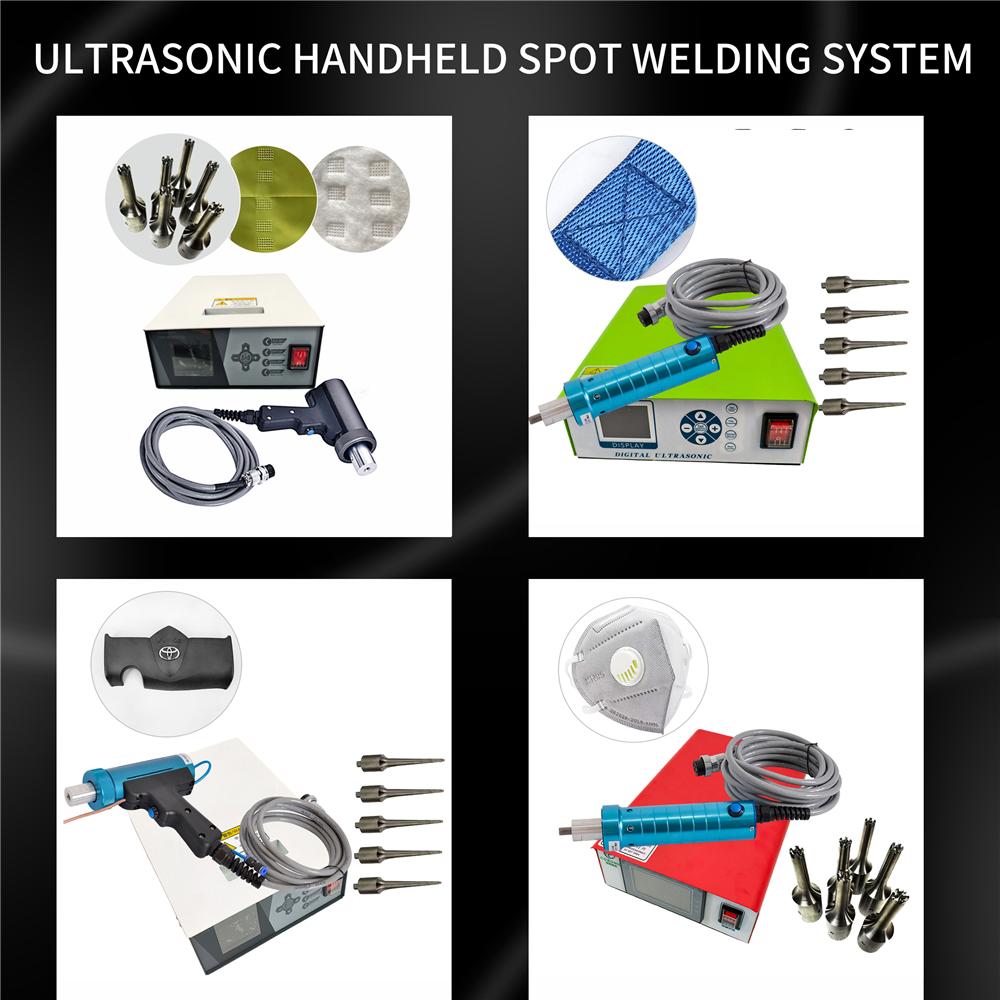