01
Customized ultrasonic molds with various frequencies
working principles
The ultrasonic die connected to the horn receives the amplified mechanical vibrations and transmits them to the material being processed. The interaction between the die and the material varies depending on the processing application:
Welding : In plastic welding, the high-frequency vibration of the mold causes the contact surface of the plastic parts to quickly generate heat through friction, causing the plastic to melt. Under pressure, the molten plastic fuses together and forms a strong welded joint after cooling. For metal welding, high-frequency vibration can remove the oxide film on the metal surface, promote the diffusion and bonding between metal atoms, and achieve solid-phase welding of metals.
Cutting : The die contacts the material to be cut under high-frequency vibration, and the high-frequency, high-energy friction and shearing action generated cause the material to partially melt or soften, thereby achieving cutting. This cutting method produces a neat cut without burrs.
Grinding and polishing : The high-frequency vibration of the mold drives the abrasive particles or polishing tools to interact strongly with the workpiece surface, accelerating material removal and surface flattening, and improving the efficiency and quality of grinding and polishing.
Cleaning : When the mold is used for cleaning, it generates high-frequency vibrations in the cleaning liquid, which generates a large number of tiny bubbles in the cleaning liquid. Under the action of ultrasound, these bubbles undergo a process of formation, growth and rapid closure, generating strong impact and cavitation effects, which can effectively remove dirt, grease and impurities on the surface of the workpiece.
Emulsification and dispersion : In industries such as chemical and food, the high-frequency vibration of the mold can disperse immiscible liquids into tiny particles, mix them evenly, and form a stable emulsion or suspension.
Product Introduction
Commonly used materials: Aluminum alloy 7075, 2024, 6061, etc., with the characteristics of high hardness, strong thermal conductivity and good toughness; titanium alloy has extremely high toughness, good thermal conductivity and high hardness, but is expensive; SCM8 is generally used for implant screws and metal inlays, with excellent toughness and high hardness.
High wear resistance: Through surface treatment methods such as spraying, electroplating, chemical treatment, etc., the hardness and smoothness of the mold surface can be improved, wear can be reduced, and the service life of the mold can be increased.
application areas
Plastic processing: used for plastic welding, such as welding of automotive interior parts, plastic containers, electronic equipment housings, etc.
Metal processing: It can realize metal welding and assist metal forming, such as aluminum, copper and other metal welding and ultrasonic assisted forging.
Cutting: Cutting plastic, rubber, leather, cloth and other materials, used in clothing, footwear, packaging and other industries.
Grinding and polishing: Grind and polish precision workpieces such as optical lenses and mold cavities to improve surface quality.
Cleaning field: cleaning electronic components, mechanical parts, jewelry, etc. to remove dirt and impurities.
Chemical food: used for emulsification and dispersion in chemical and food industries, such as preparation of cosmetic emulsions and food suspensions.

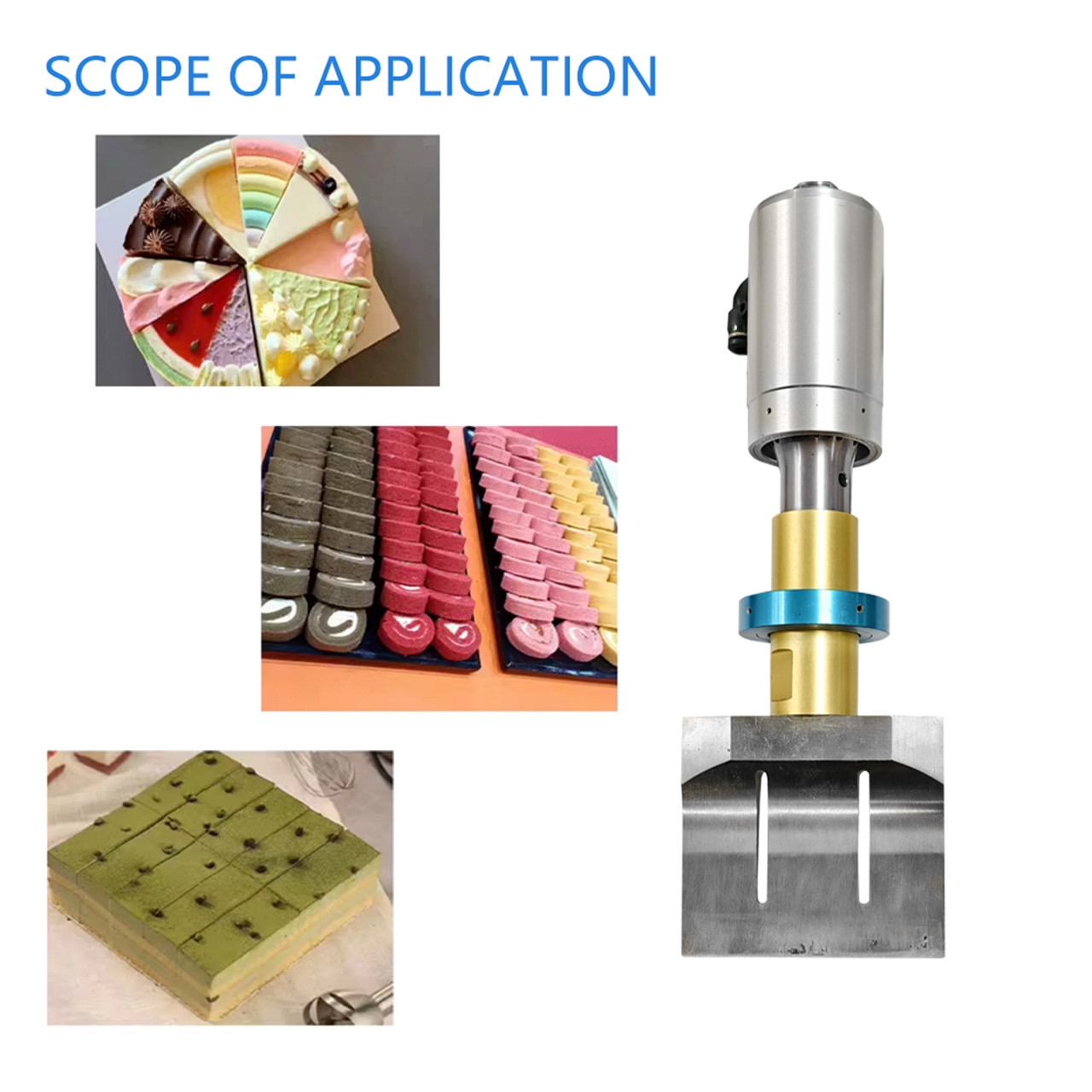
details display
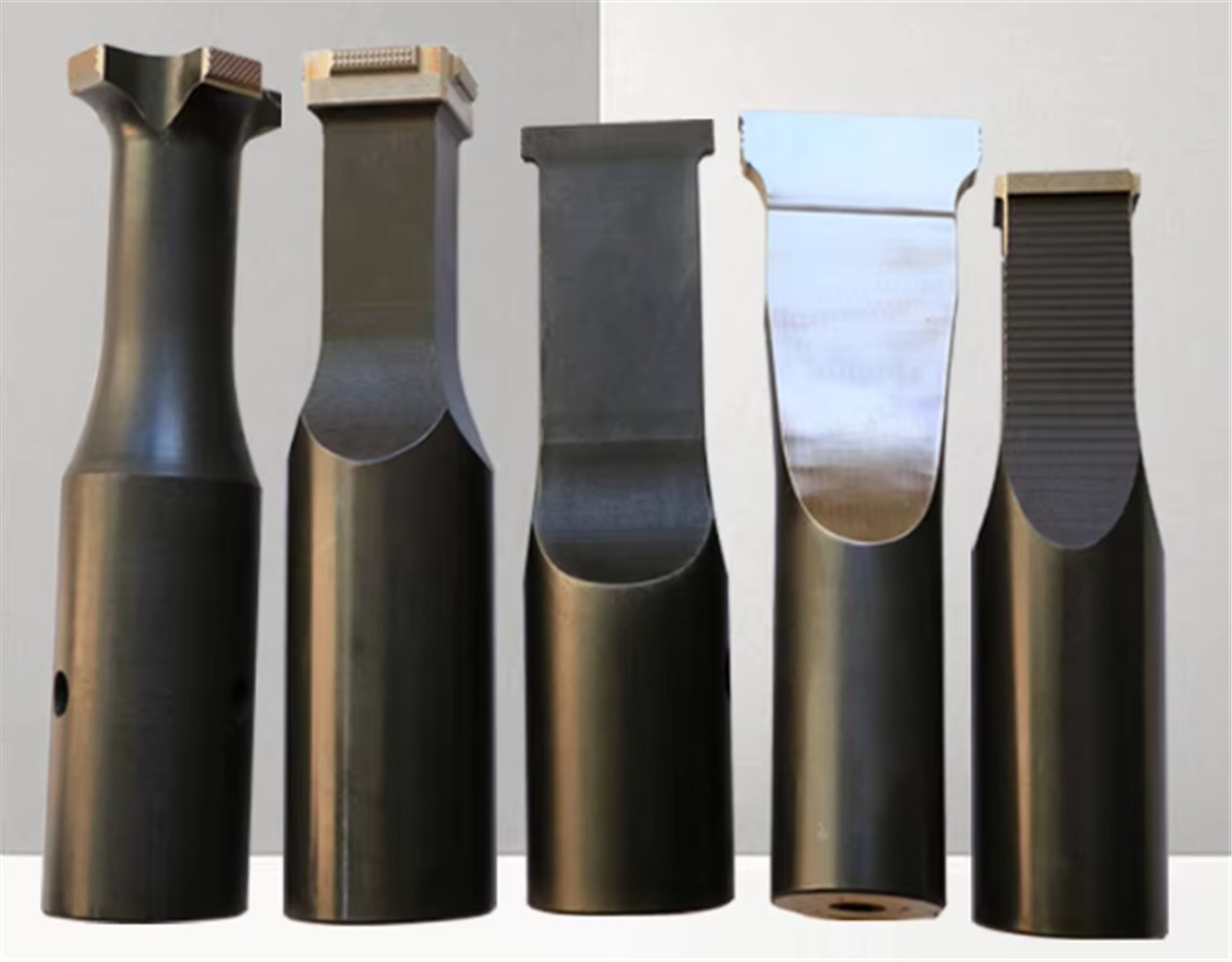
Product Parameters
Operating frequency |
15KHz/20KHz/28KHz/30KHz/40KHz |
Output Power |
/ |
Input voltage |
/ |
Amplitude adjustment |
/ |
Welding time |
0.1~1 |
Machine size |
Customized |
Machine weight |
Customized |
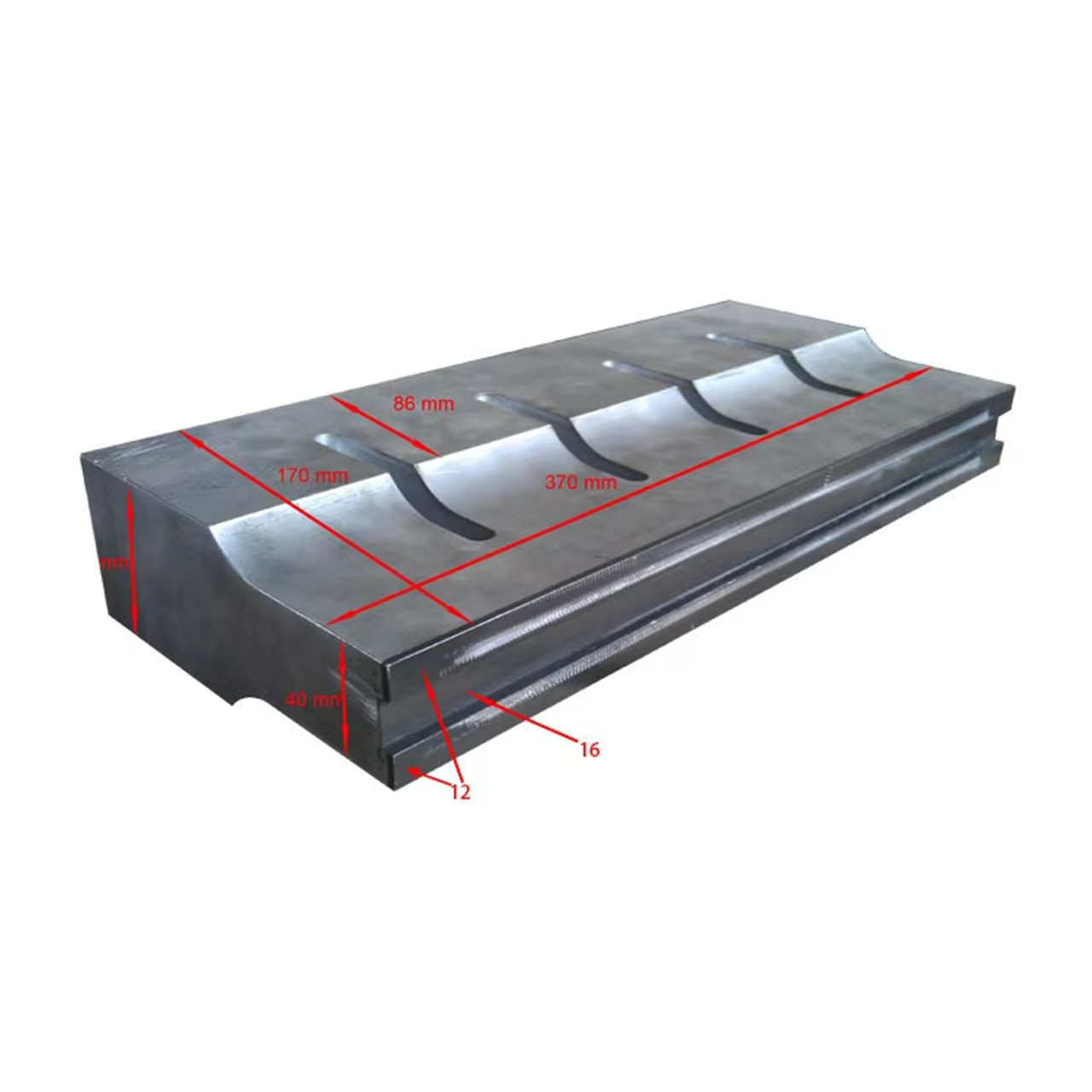
Machine maintenance
Appearance cleaning: After each use, use a soft cloth dipped in mild detergent to carefully wipe the surface of the mold to remove residual materials and stains to avoid corrosion of the mold and affect subsequent processing results.
Wear inspection: Regularly check the mold surface and working parts to see if there is wear, scratches, or deformation. Once severe wear or damage to key parts is found, they must be replaced in time to ensure processing accuracy and quality.
Connection parts: Check the connection parts between the mold and the horn and the main body of the equipment to ensure that the screws, nuts and other connectors are tightened to prevent loosening that may cause abnormal ultrasonic energy transmission and affect processing efficiency and mold life.
Ultrasonic system related maintenance: Because the mold is part of the ultrasonic system, it is necessary to check whether the generator parameters are stable and whether the transducer is working properly to ensure that the mold works in a suitable ultrasonic environment.
Storage requirements: If the mold is not used for a long time, it needs to be cleaned and dried, and placed in a dry, ventilated environment without corrosive gases to avoid moisture, rust, and corrosion by chemicals.
After-Sales Service
We provide a one-year warranty service for our products and will fully protect your usage rights during the warranty period. In addition, if you encounter any questions or technical issues during use, our profession al online technical support team will be available to answer your questions and provide you with efficient and thoughtful solutions.