01
Fully automatic wireless ultrasonic edging machine
Working Principle
When the ultrasonic lace machine works, the first step is for the electronic oscillator to convert the AC power into a high-frequency electrical signal, usually with a frequency between 20kHz and 40kHz. High frequency electrical signals are transmitted to the transducer, which utilizes the piezoelectric effect to convert the electrical signals into mechanical vibrations of the same frequency. The vibration is amplified by the amplitude lever and transmitted to the welding head. When the welding head comes into contact with the processing material, such as non-woven fabric, synthetic fabric, etc., high-frequency vibration causes the internal molecules of the material to rub at high speed, instantly generating heat. The material rapidly melts or softens under the action of heat. At this time, under the pressure of the welding head, processing operations such as welding, cutting, or embossing are achieved. After leaving the welding head, the material cools and solidifies, completing the processing process.
Product Introduction
Ultrasonic lace machine is a device that uses ultrasonic technology for fabric processing, widely used in industries such as textiles, clothing, and home furnishings.
Its working principle is to convert AC power into high-frequency electrical signals through an electronic oscillator, and the transducer converts the electrical signals into mechanical vibrations, which are then amplified and transmitted to the welding head through a variable amplitude rod. When the welding head contacts the material, high-frequency vibration causes internal molecular friction and heat generation, achieving processing such as welding, cutting, embossing, etc.
This device has obvious advantages, with efficient and energy-saving processing, the ability to complete operations instantly, and low energy consumption; Excellent processing quality, neat and smooth lace edges, exquisite patterns; Strong material adaptability, suitable for various materials such as synthetic fibers and non-woven fabrics; Easy to operate, highly automated, and user-friendly for beginners; At the same time, it is environmentally friendly and safe, with no chemical emissions and multiple protections.
In practical applications, ultrasonic lace machines can be used to produce clothing lace, curtain decoration, bedding edging, mask ear band welding, etc., providing efficient and high-quality processing solutions for various industries.
application area
Clothing industry: used for lace production of collars, cuffs, skirts, pant legs, and other parts of various clothing, as well as embossing treatment of decorative patterns to enhance the beauty and fashion sense of clothing.
In the field of home textiles, edge decoration and splicing of curtains, tablecloths, and bedding are used to create exquisite lace and enhance the decorative effect of home textile products.
Medical supplies: used in mask production for welding ear bands; When making disposable medical supplies such as surgical gowns and medical bed sheets, sealing and edge treatment are carried out to ensure the sterility and safety of the products.
Packaging industry: Sealing and embossing of flexible packaging for food, cosmetics, gifts, etc. to make the packaging more attractive while ensuring the sealing of the packaging.
Automotive Interior: Processing interior components such as car seat covers, floor mats, sun visors, etc. to achieve beautiful lace decorations and secure splicing.
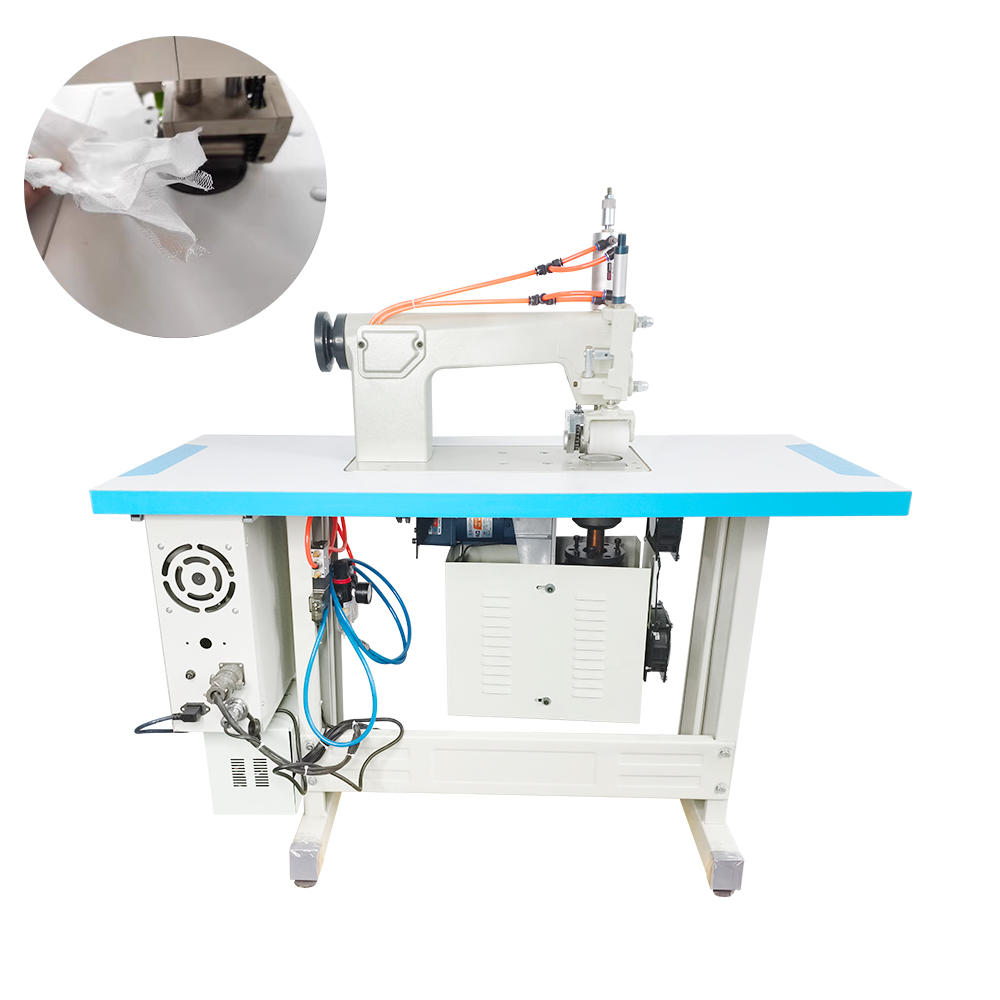
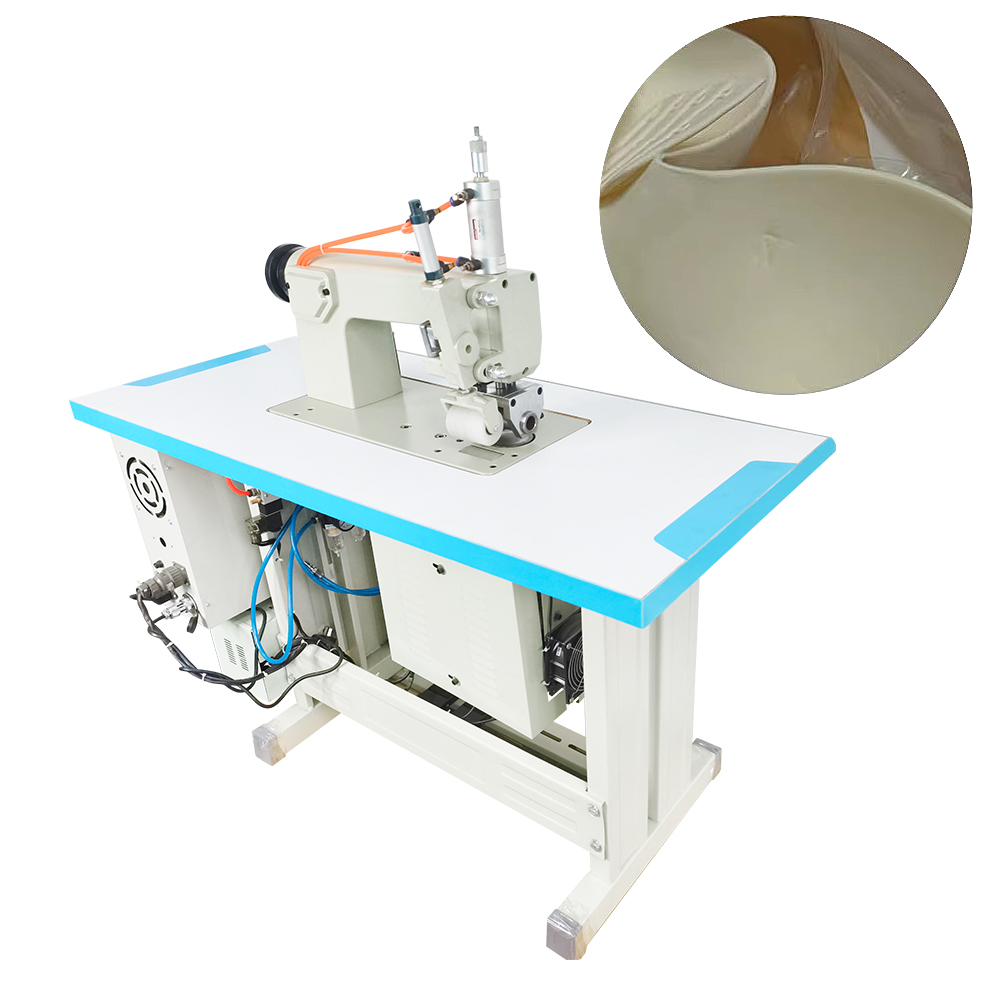
Detail Display
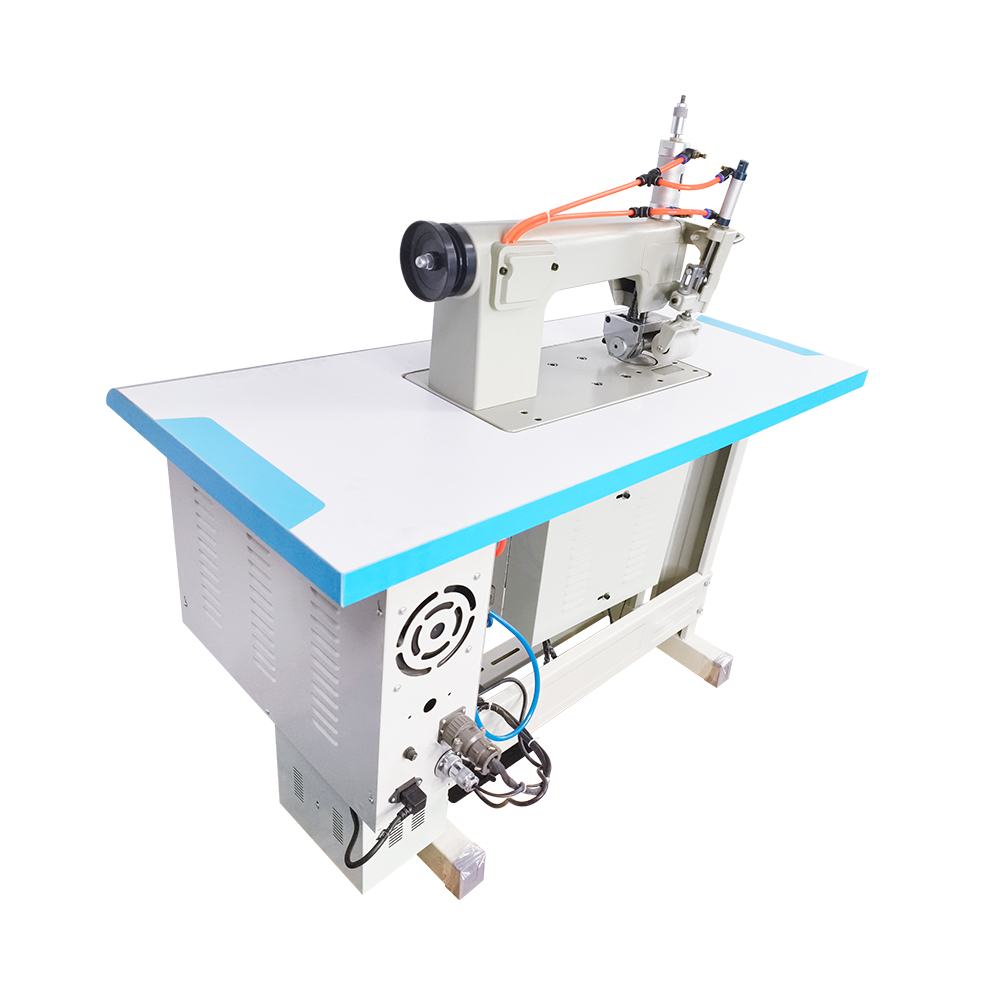
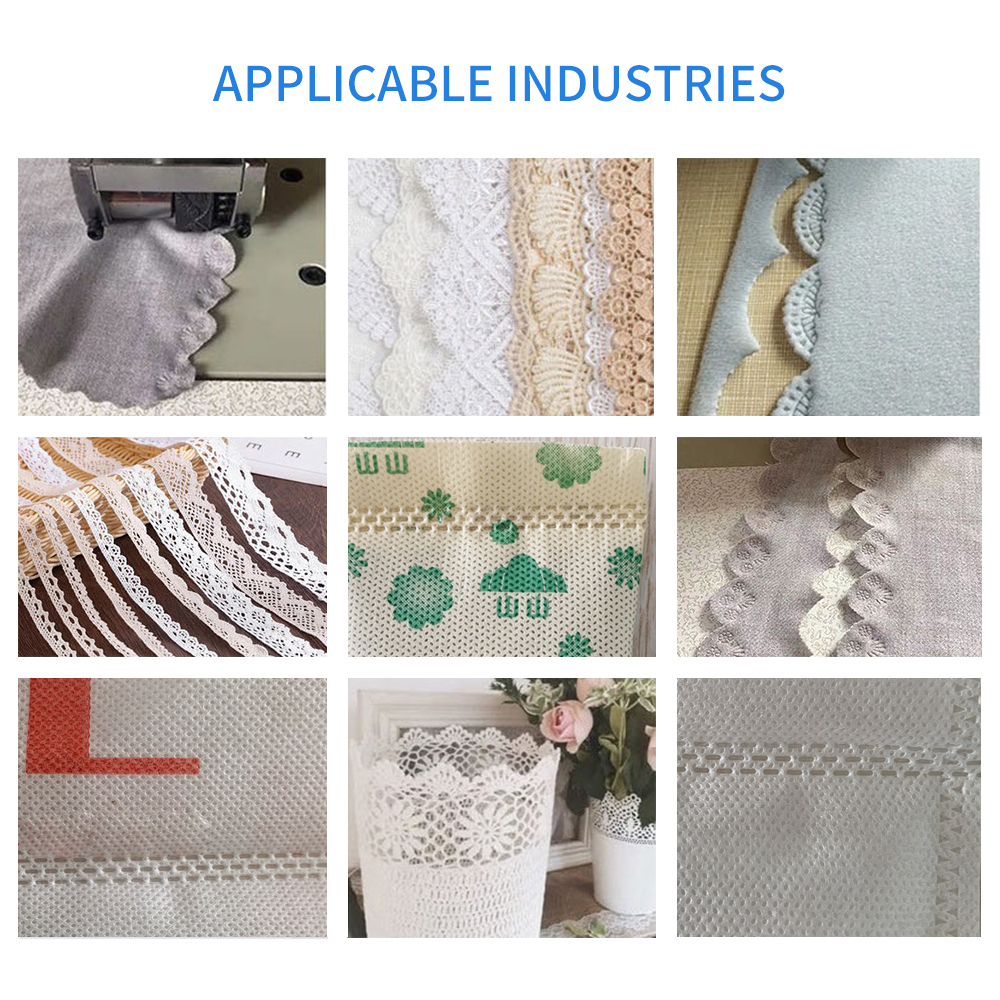
Mold customization
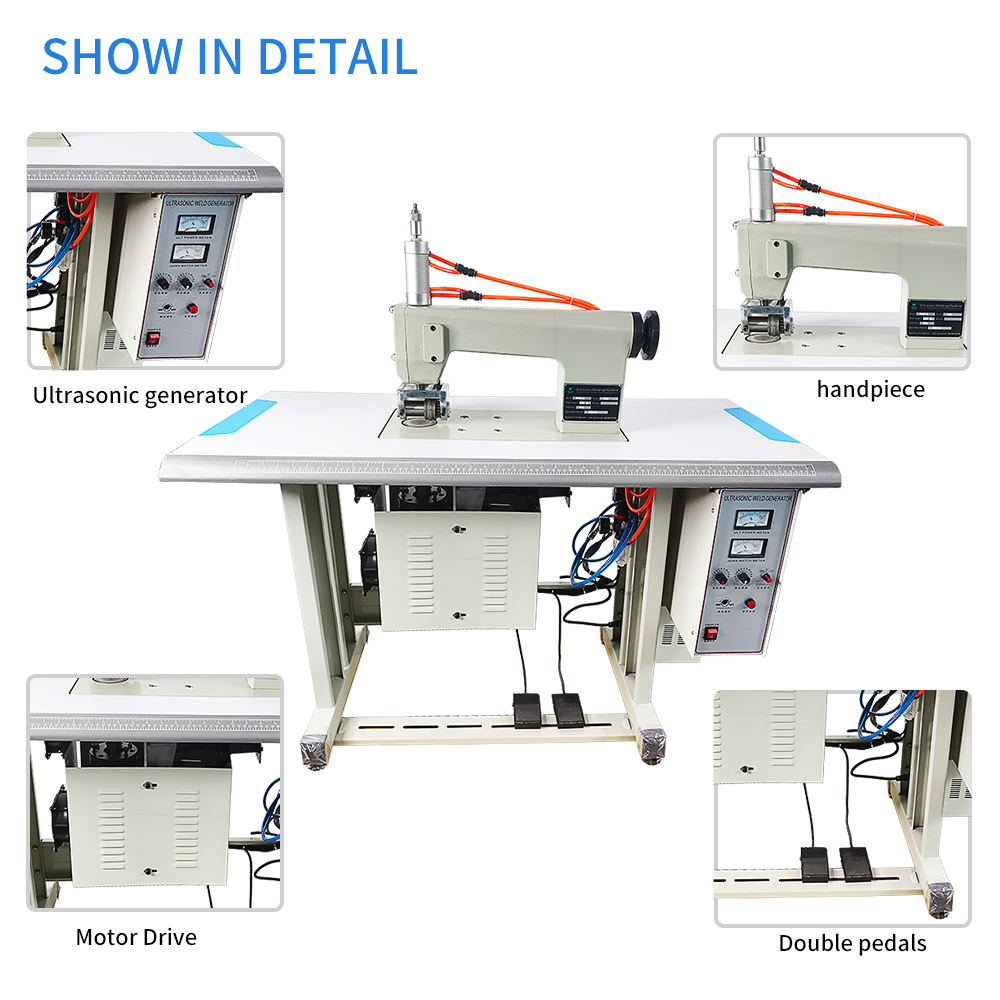
Operating Frequency |
28KHz/35KHz/40KHz |
Output Power |
600~1500W |
Input Voltage |
AC220v 50Hz |
Amplitude Adjustment |
1%~100% |
Weld Time |
0.01~9.99s |
Connect To Air Pressure |
0.1~0.7MPa |
Machine maintenance and upkeep
Mechanical components: Regularly add lubricating oil to transmission components (such as pulleys, chains, etc.) to ensure smooth operation; Check the tension of the belt to avoid slipping or breakage; Check the screws at each connection point and tighten any loose screws in a timely manner.
Electrical system: Check the circuit for damage and aging, prevent leakage and short circuit; Regularly clean the dust inside the electrical box to ensure good heat dissipation; Check if the control buttons are working properly and replace damaged buttons in a timely manner.
Ultrasonic system: Keep the working environment of the ultrasonic generator dry and avoid moisture; Regularly check the parameter settings of the generator to ensure that the frequency and power are normal; Check if the connection between the transducer and the amplitude rod is secure, free from cracks or damage.
Flower wheel and bottom mold: After each use, clean the residue on the flower wheel and bottom mold in a timely manner to prevent material accumulation from affecting the lace effect; Regularly check the wear of the flower wheel, and replace it in a timely manner if it is severely worn; Adjust the gap between the flower wheel and the bottom mold to ensure even pressure.
Regular testing: Regularly conduct overall performance testing on the equipment, such as ultrasonic output intensity, lace forming quality, etc., to ensure stable operation of the equipment.
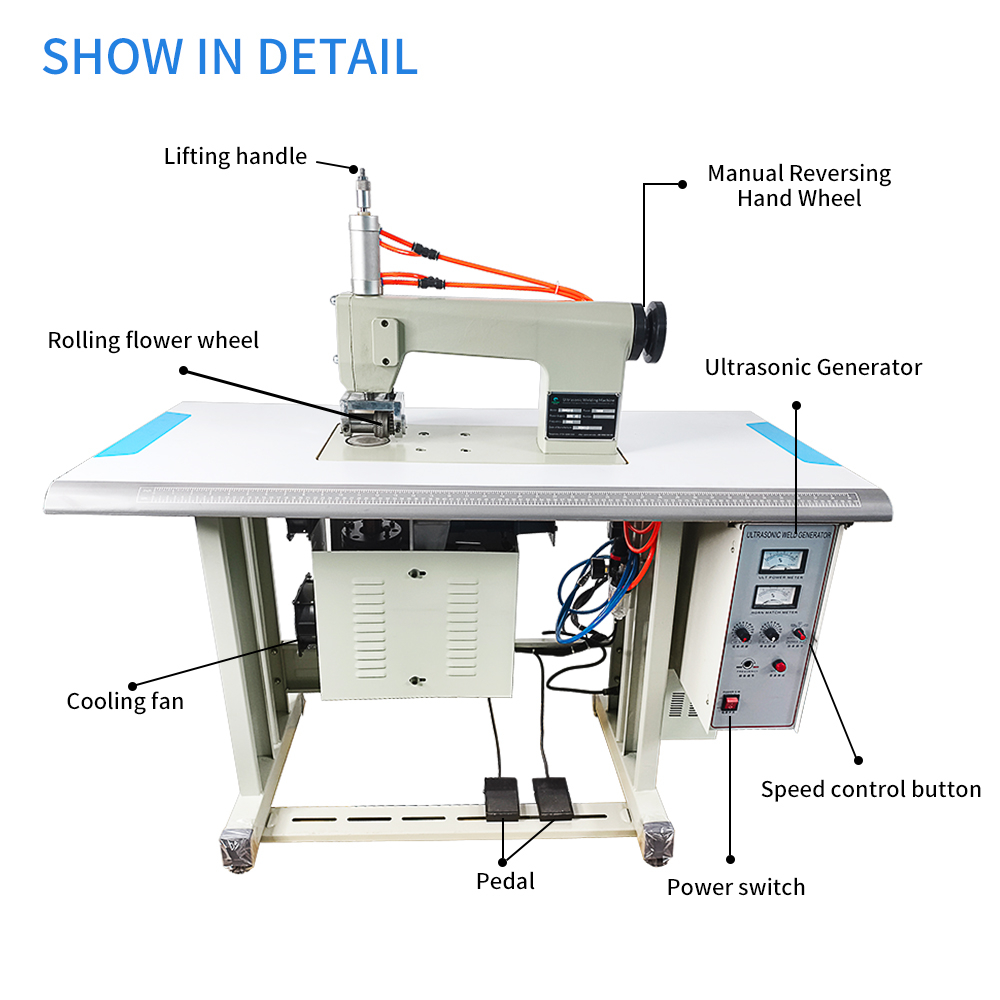
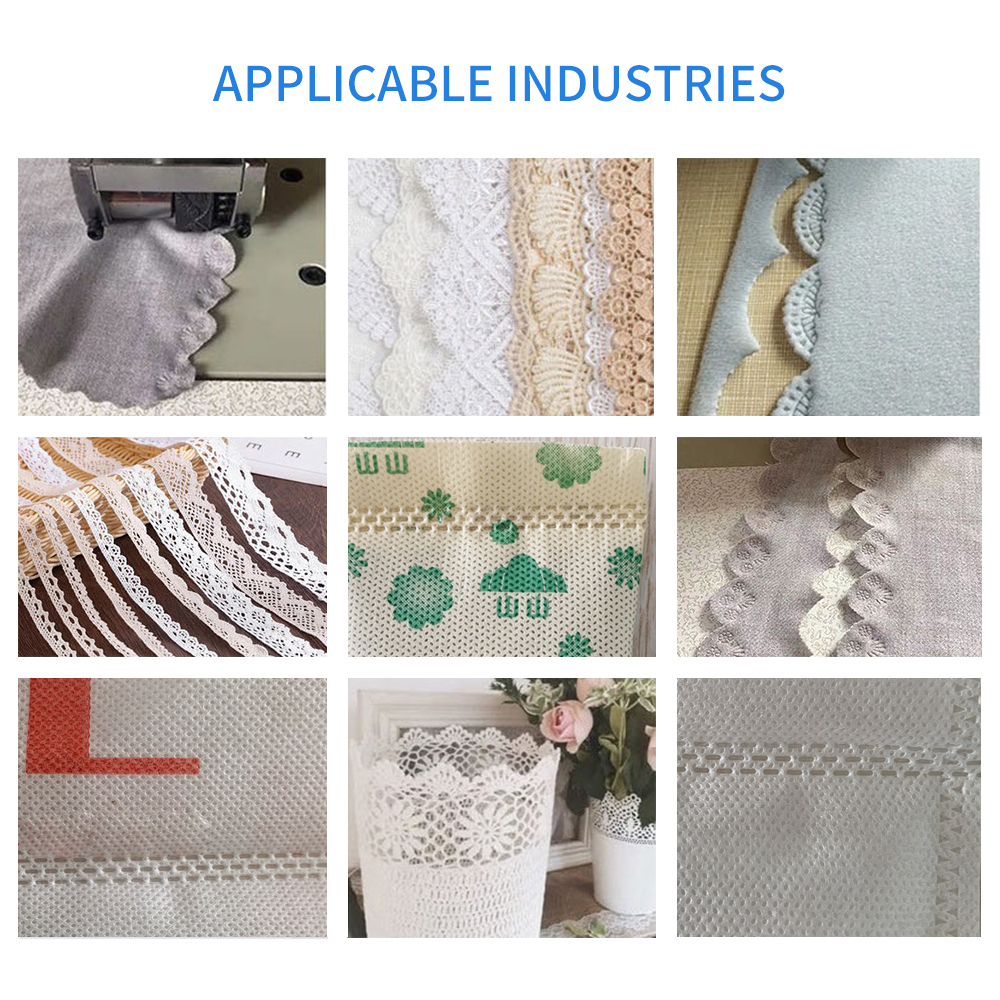