01
Metal welding machine for copper wire welding and cutting
Brief Description (Core Features)

Low-Temperature Welding: No high-temperature metal melting required, minimizing impact on the base material's properties and avoiding issues like deformation or brittleness caused by high heat.
Eco-Friendly and Clean: No flux or filler materials are used, eliminating harmful gases and slag, meeting environmental standards, and reducing post-welding cleaning processes.
High Welding Quality: Welded joints exhibit high strength and excellent sealing, suitable for applications with stringent welding quality requirements.
Strong Adaptability: Capable of welding various metal materials, including similar or dissimilar metals such as copper-aluminum, nickel-stainless steel, etc.
3. Working Principle
During operation, the ultrasonic metal welding machine converts mains electricity into high-frequency AC signals via an ultrasonic generator. The ultrasonic transducer then transforms these electrical signals into high-frequency mechanical vibrations using piezoelectric or magnetostrictive effects. The vibrations are amplified by a booster and transmitted to the welding head, which acts on the workpiece. The high-frequency vibrations generate frictional heat on the metal surfaces, removing oxide layers and enabling atomic diffusion and fusion to achieve a solid-state bond.
4. Product Introduction
The ultrasonic metal welding machine converts mains electricity into high-frequency electrical signals via an ultrasonic generator, which are then transformed into high-frequency mechanical vibrations by a transducer. These vibrations are transmitted through a booster and welding head to the workpiece, generating frictional heat and atomic fusion for welding. With features like low-temperature operation, eco-friendliness, high welding quality, and broad material compatibility, it is widely used in electronics, automotive, aerospace, and new energy industries, enabling efficient metal joining across various sectors.
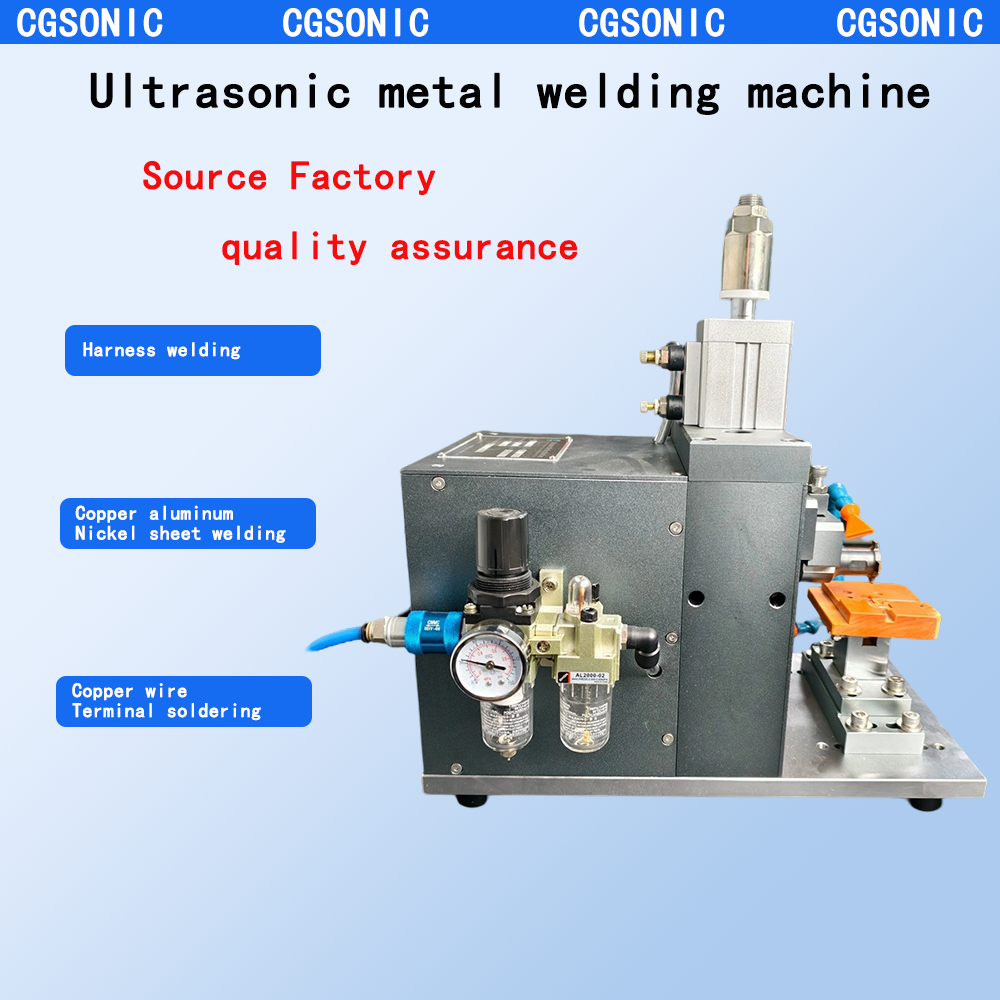
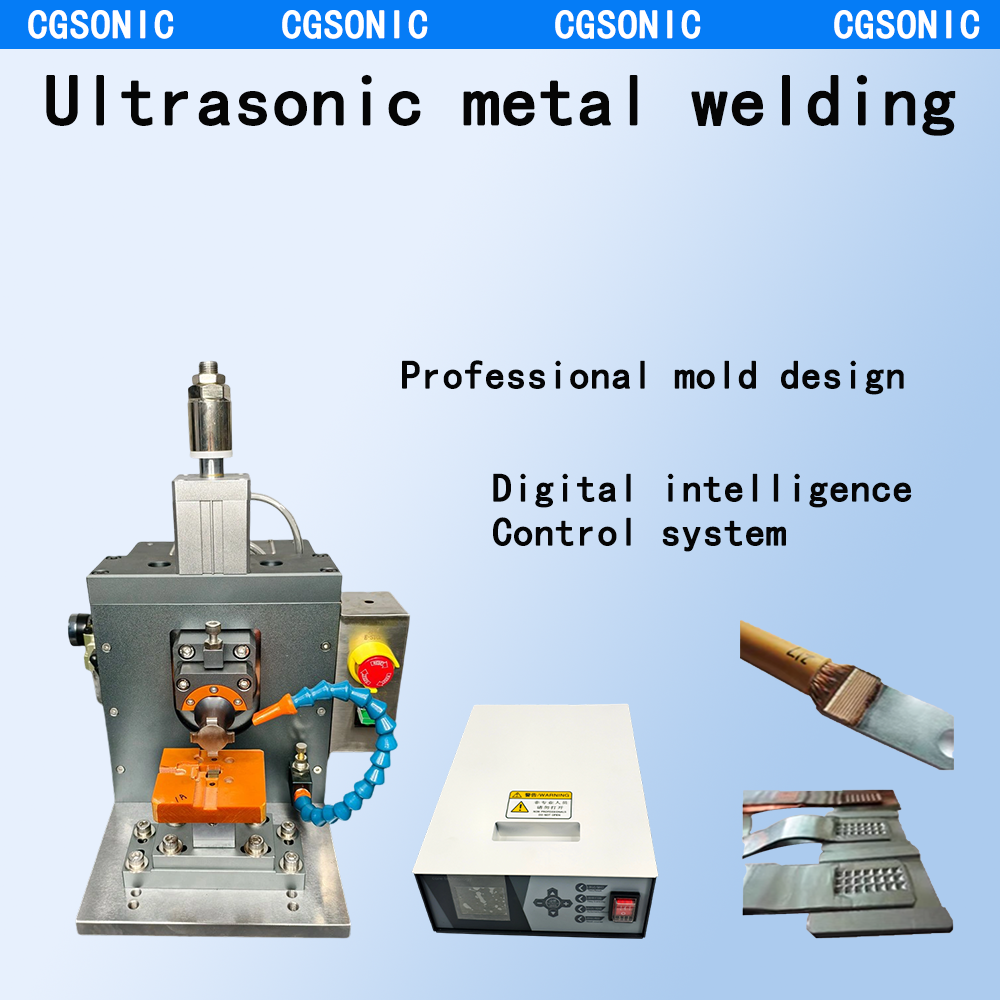
Application Fields
Electronics Industry: Used for welding battery tabs and terminals, electronic components to circuit boards, and micro-motor manufacturing, ensuring miniaturization and high performance of electronic products.
Automotive Industry: Suitable for welding wire harnesses, sensors, and electronic modules, meeting lightweight and reliability requirements.
Aerospace: Employed in manufacturing aircraft engine components and structural parts, ensuring welding quality and structural integrity in extreme environments.
New Energy Sector: Facilitates efficient metal joining in solar panel production and energy storage devices, supporting the development of the new energy industry.
6. Compatible Molds
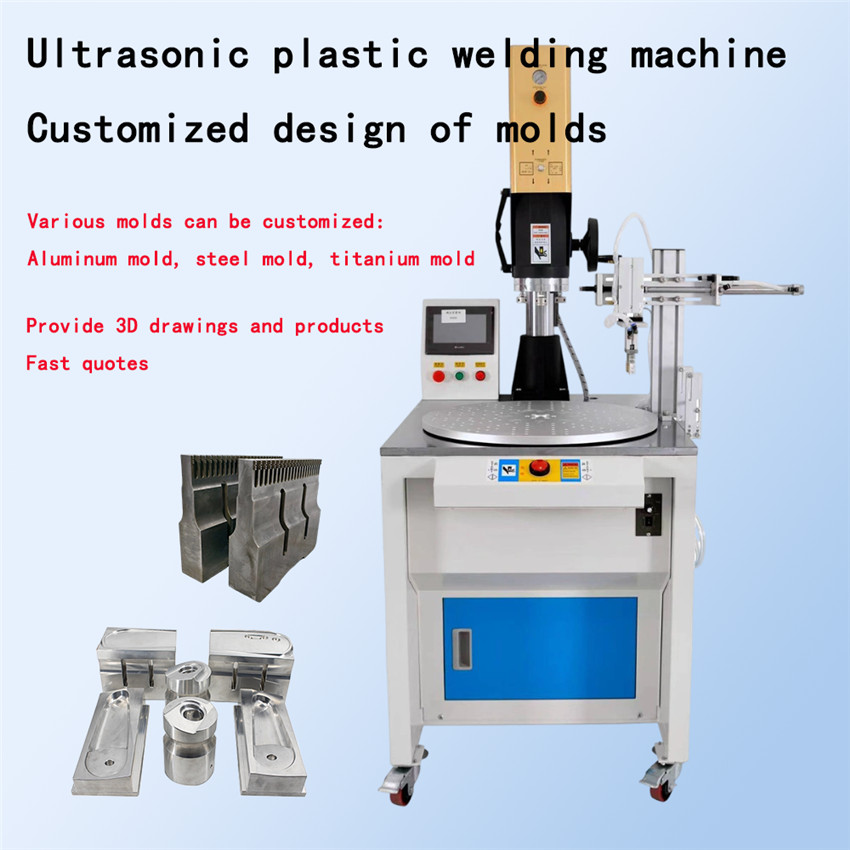
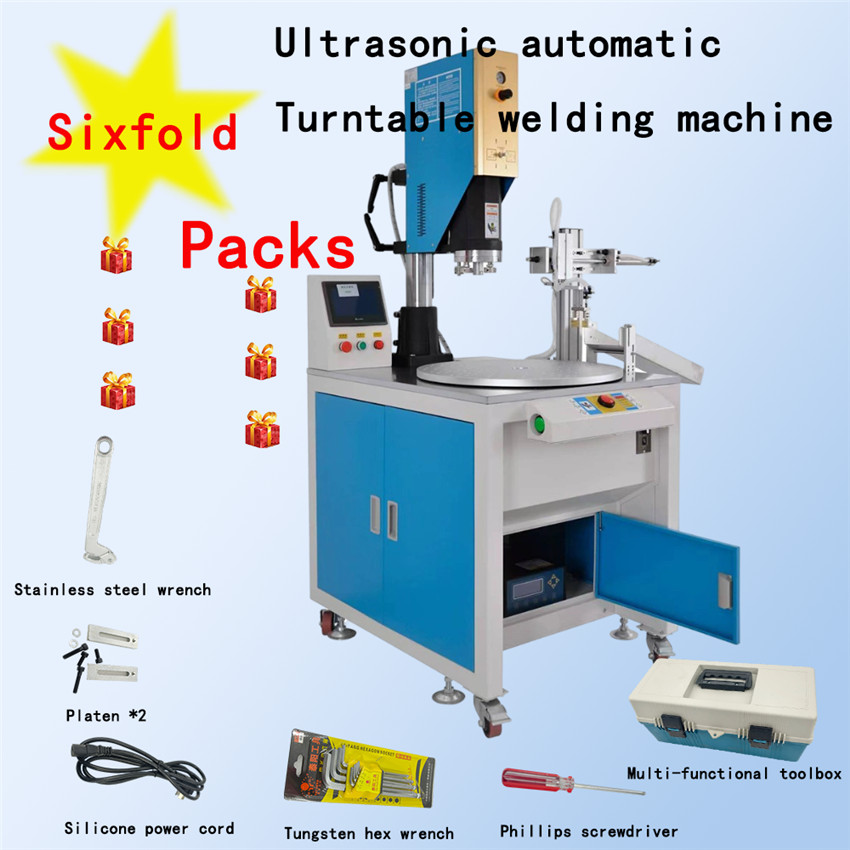
Product Parameters
Parameter |
Specification |
Working Frequency |
20KHz/35KHz |
Output Power |
1500–3000W |
Input Voltage |
AC220V 50Hz |
Amplitude Adjustment |
1%–100% |
Welding Time |
0.01–9.99s |
Machine Dimensions |
468×330×452mm / 400×354×430mm |
Machine Weight |
30.2kg / 27.7kg |
Air Pressure Requirement |
0.1–0.7MPa |
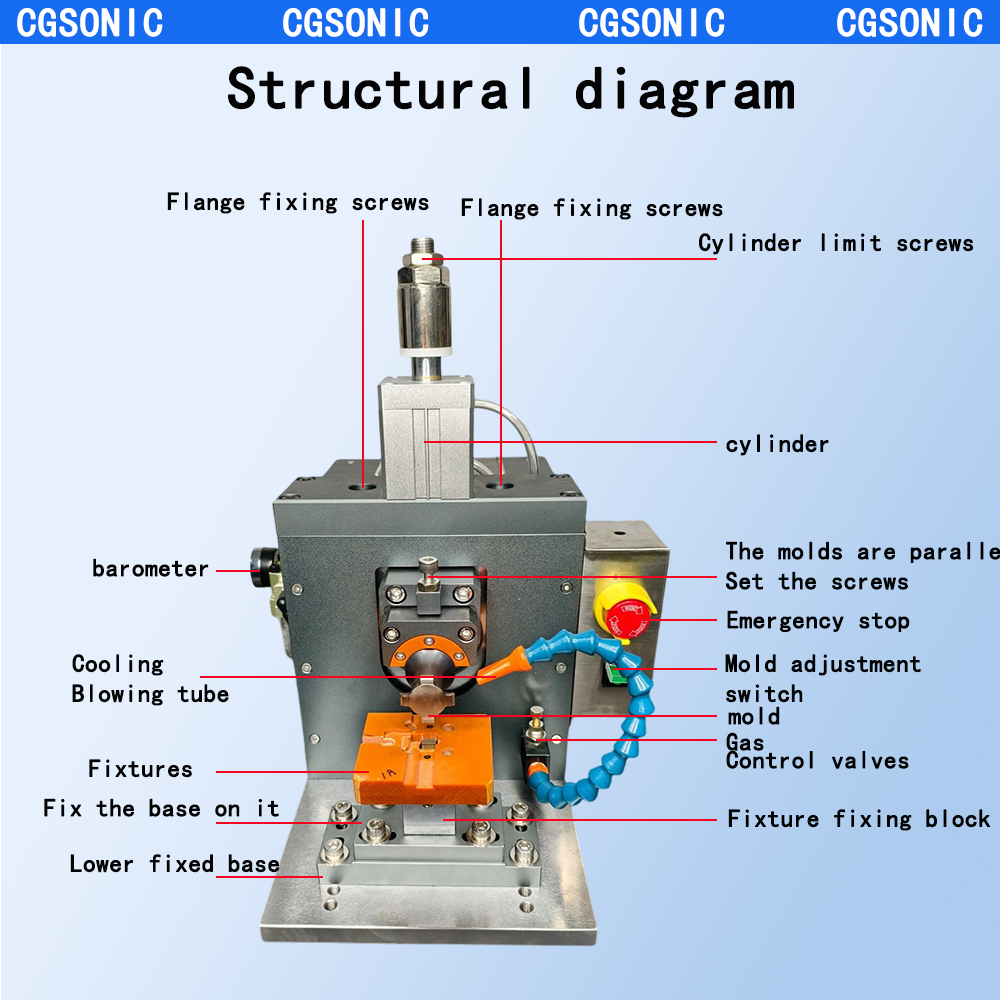
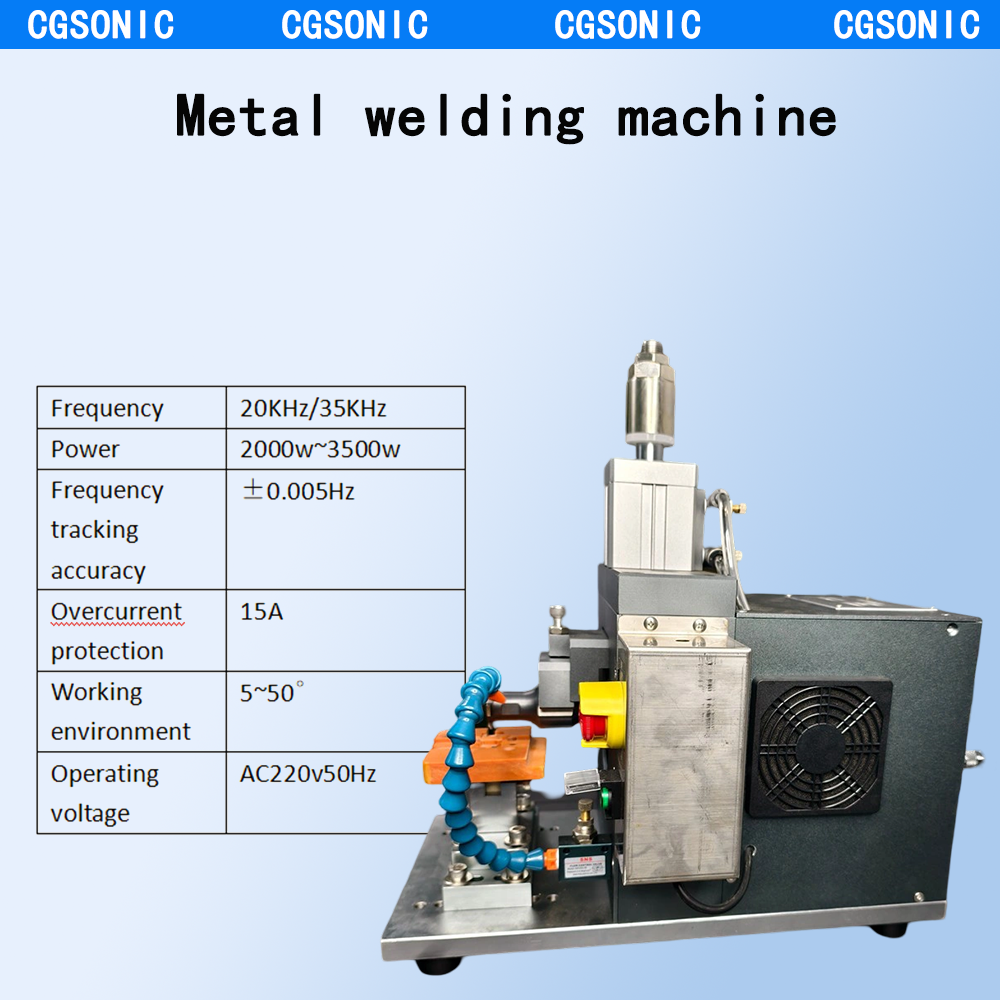
Machine Maintenance
Mechanical Components: Regularly lubricate transmission parts such as lead screws, rails, and sliders to reduce wear and ensure smooth operation. Check the clamping force of fixtures and adjust or replace worn clamping blocks to secure workpieces during welding. Inspect bolts at mechanical connections and tighten them if loose.
Electrical System: Inspect wiring for damage or aging to prevent short circuits or leakage. Clean dust from the electrical cabinet to ensure proper heat dissipation. Verify the functionality of control buttons and displays, repairing or replacing faulty components promptly.
Ultrasonic System: Keep the ultrasonic generator in a dry environment to avoid moisture. Regularly check parameter settings to ensure stable output power and frequency. Inspect the connections between transducers and boosters for cracks or wear, addressing issues immediately.
Welding Tools: Clean welding head surfaces of metal residues after each use to maintain welding quality. Regularly inspect welding heads for wear and replace them if necessary.
Periodic Testing: Conduct comprehensive performance tests, including welding strength, time, and energy control, to ensure optimal operation.
After-Sales Service
We provide a one-year warranty service for our products and will fully protect your usage rights during the warranty period. In addition, if you encounter any questions or technical issues during use, our professional online technical support team will be available to answer your questions and provide you with efficient and thoughtful solutions.