Our company has ultrasonic (plastic welding, metal welding), ultrasonic cutting, water nozzle machine, and homogenizer.
2025-04-30
Shenzhen Chengguan Intelligent Ultrasonic Equipment Co., Ltd. is deeply engaged in the field of ultrasonic equipment, with a rich and diverse product matrix that can fully meet the needs of various industries. Our company has ultrasonic (plastic welding, metal welding), ultrasonic cutting, water nozzle machine, and homogenizer.
Ultrasonic plastic welding is an efficient and environmentally friendly connection technology with wide applications in multiple fields. The following are some of the main areas:
Automotive industry
Interior parts: The dashboard, door interior panels, seats and other components of a car are usually composed of various plastic materials. Ultrasonic plastic welding can firmly connect these components together, not only improving production efficiency, but also ensuring the strength and sealing of the connection, while making the appearance of the product more beautiful.
Exterior parts: Ultrasonic plastic welding technology is often used for car bumpers, headlight housings, and other exterior parts. This welding method can achieve seamless connection between plastic components, improve the waterproof and dustproof performance of the components, and enhance the overall strength and durability of the exterior parts.
Engine peripheral components: Some plastic parts in the engine, such as the intake manifold and oil pan, require high sealing and strength. Ultrasonic plastic welding can achieve reliable connection without damaging the performance of plastic components, ensuring that these components can withstand harsh environments such as high temperature and high pressure during engine operation.
Electronic appliances
Consumer electronics products: The casing of consumer electronics products such as mobile phones, tablets, laptops, etc. is usually made of plastic material. Ultrasonic plastic welding can tightly connect the various parts of the casing to form a whole, protecting the internal electronic components. In addition, some internal structural components of electronic products, such as battery boxes and speaker brackets, are also assembled using ultrasonic plastic welding technology.
Home appliances: Ultrasonic plastic welding is widely used in connecting plastic components of products such as washing machines, refrigerators, and air conditioners. For example, the assembly of components such as the control panel of a washing machine, the inner compartment of a refrigerator, and the outer shell of an air conditioner can all be achieved through ultrasonic plastic welding to improve product quality and stability.
Packaging industry
Plastic containers: Ultrasonic plastic welding is commonly used for sealing and connecting containers in the production process of various plastic bottles, plastic boxes, plastic buckets, and other packaging containers. Through ultrasonic welding, rapid sealing of plastic containers can be achieved, ensuring the sealing and integrity of packaging and preventing leakage of contents.
Plastic film: In the packaging application of plastic film, ultrasonic plastic welding can be used for film sealing and cutting. This welding method can achieve high-speed sealing of the film, with good sealing quality and less leakage. At the same time, it can accurately cut the film according to needs, improving packaging efficiency and quality.
Medical devices
Medical consumables: Ultrasonic plastic welding is widely used for the connection and packaging of plastic components in the production of medical consumables such as syringes, infusion sets, and blood collection devices. This welding method can ensure the sealing and sterility of medical consumables, ensuring the safety and reliability of the product during use.
Medical device casing: The casing of medical devices usually requires good sealing, stability, and aesthetics, and ultrasonic plastic welding can meet these requirements. Through ultrasonic welding technology, various parts of the medical device casing can be connected as a whole, improving the strength and stability of the casing while ensuring the appearance quality.
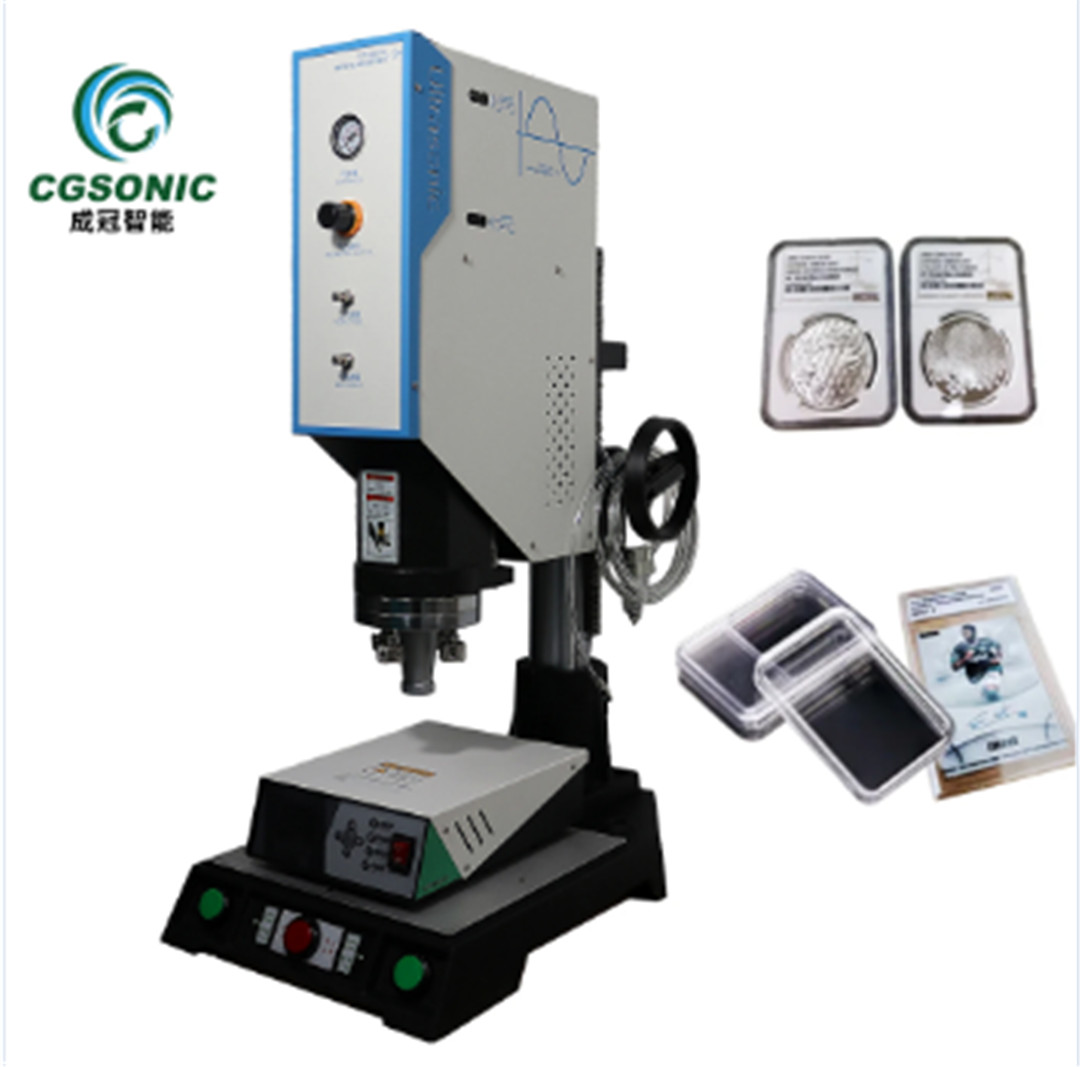
Ultrasonic metal welding is a solid-state welding technology that has important applications in multiple fields. The following are some of the main application areas:
Electronic and electrical field
Battery manufacturing: used in the production of lithium batteries to connect battery terminals and terminals. It can achieve reliable connection of metal materials such as aluminum and copper, ensure good electrical connection performance inside the battery, and improve the charging and discharging efficiency and safety of the battery. In addition, in the production of other types of batteries such as nickel hydrogen batteries and lead-acid batteries, the connection between electrodes and wires is also commonly used.
Electronic component assembly: For some micro electronic components such as chip resistors, capacitors, etc., the connection between their pins and the circuit board can be achieved through ultrasonic metal welding. This welding method can achieve high-precision connection without damaging the components, ensuring the stability and electrical performance of electronic components on the circuit board. In the field of semiconductor packaging, it can also be used to connect chip pins and packaging frames.
Wire and cable connection: Suitable for connecting wires and cables of different specifications, especially for some thin wires and multi strand wires, the connection effect is significant. The metal core wires of wires and cables can be welded together, with a firm connection and low resistance, which can effectively reduce energy loss during transmission. It is commonly used for connecting internal circuits such as household appliances and automobiles, as well as for cable branch connections in power systems.
Automotive industry field
Automotive wiring harness: There are a large number of wiring harnesses inside the car that are used to transmit power and signals. Ultrasonic metal welding can connect wires of different specifications and materials together to form complex wire harness structures. The welded wire harness connection points have high reliability and can withstand vibrations and various harsh environments during the driving process of the car, ensuring the stable operation of the car's electrical system.
Engine components: In the engine, some metal components such as pistons, connecting rods, etc. have wear-resistant coatings or reinforcement ribs on their surfaces, which can be connected to the substrate through ultrasonic metal welding. This connection method can ensure the bonding strength between the coating or reinforcement and the substrate, improve the wear resistance and service life of the components. In addition, it can also be used for connecting engine sensors.
Automobile body: Ultrasonic metal welding technology is also used for the connection of some aluminum alloy or high-strength steel components in the automobile body. For example, the splicing of aluminum alloy profiles in the body frame can achieve high-strength connections, reduce body weight, and improve the fuel economy and performance of the car.
Aerospace field
Aircraft engine: In the manufacturing of aircraft engines, it is used to connect engine blades with discs, combustion chamber components, etc. It can ensure the reliability and stability of the connection under extreme conditions such as high temperature, high pressure, and high speed, ensuring the performance and safety of the engine. In addition, it can also be used for connecting metal pipes and joints in engine fuel systems.
Aircraft structural components: Ultrasonic metal welding technology has unique advantages in connecting metal materials such as aluminum alloys and titanium alloys in the wings, fuselage, and other structural components of an aircraft. It can achieve high-quality connections, reduce welding defects, improve the strength and fatigue performance of structural components, while reducing structural weight, which is of great significance for improving the performance and economy of aircraft.
Other fields
Metal foil processing: In the production and processing of metal foil, it is commonly used to connect the metal foil into the required length or shape. For example, in capacitor production, aluminum foil or copper foil is welded into electrodes; In the production of solar cells, metal electrodes are used to connect photovoltaic cells. It can achieve precise welding of ultra-thin metal foil materials, ensuring connection quality and electrical performance.
Jewelry manufacturing: In jewelry processing, it can be used to weld metal chains, buckles, inlay brackets, and other components. Ultrasonic metal welding can achieve a firm connection of metal components without damaging the surface of jewelry and gemstones, and the welding points are aesthetically pleasing, meeting the high-quality requirements of jewelry.
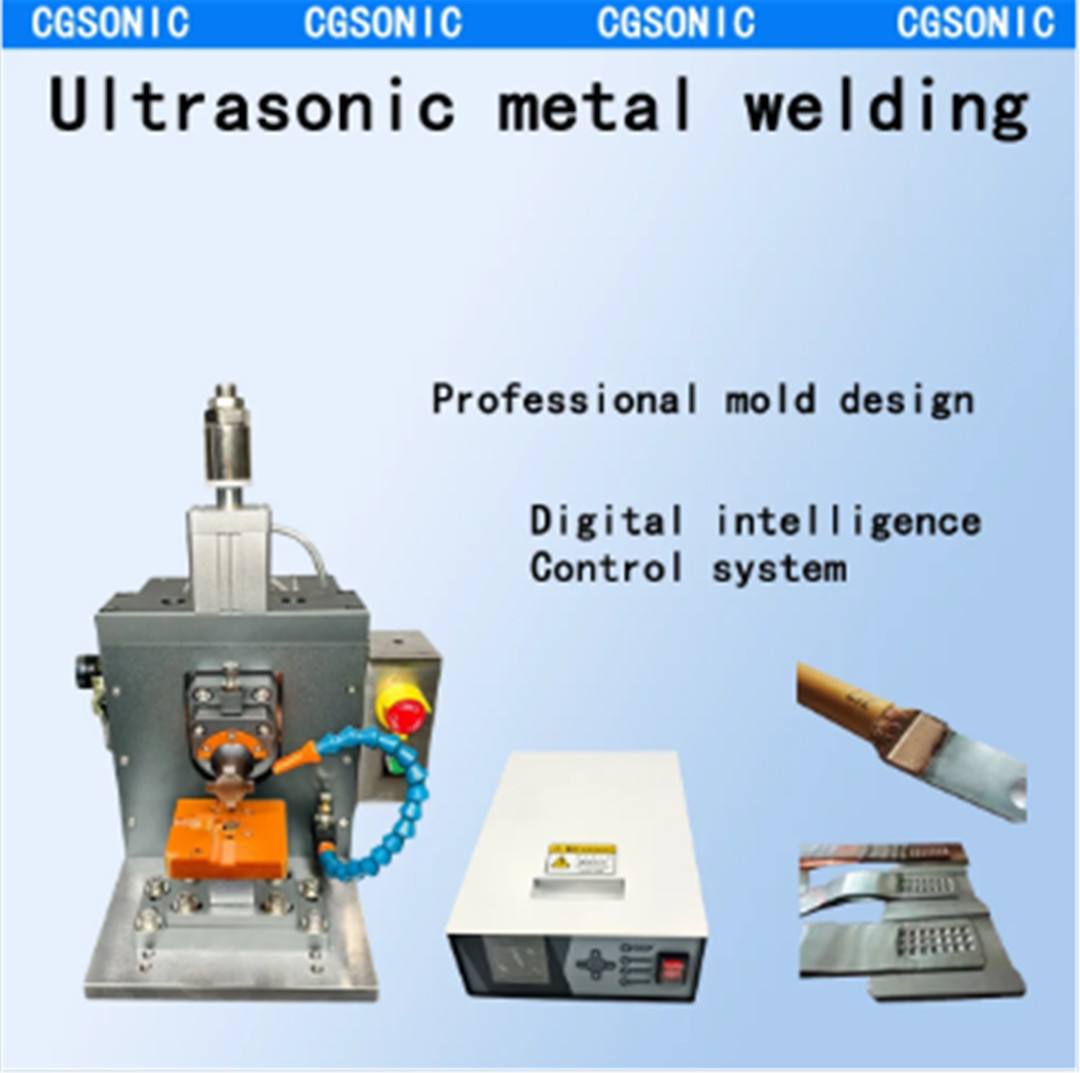
Ultrasonic cutting has the advantages of smooth incision, high precision, and minimal thermal impact, and is widely used in the following fields:
Food processing industry
Baked goods: used for cutting baked goods such as bread, cakes, cookies, etc. Can cut bread into thin slices of uniform thickness, with smooth cuts that will not damage the internal structure of the bread; For multi-layer cakes, precise cutting is possible to maintain the shape and layers of the cake.
Meat processing: When cutting meat, it can effectively avoid tearing of meat fibers, keep the incision neat, reduce juice loss, and help maintain the freshness and nutritional content of the meat. It can also be used for cutting frozen meat. Compared to traditional cutting tools, ultrasonic cutting is more labor-saving and has a faster cutting speed.
Candy chocolate: For soft and sticky candies such as gummies and toffee, ultrasonic cutting can accurately cut them into the desired shape and size without sticking to the blade, ensuring the appearance quality of the candy. When cutting chocolate, high-precision cutting can be achieved to meet the production needs of chocolate products with different shapes and specifications.
Plastic processing industry
Plastic film cutting: During the cutting process of plastic film, ultrasonic cutting can achieve high-speed and precise cutting, with smooth and burr free cuts that do not generate static electricity, avoiding adhesion and curling of the film, and improving the cutting quality and production efficiency of the film.
Plastic sheet cutting: For plastic sheets of various thicknesses, such as PVC sheets, acrylic sheets, etc., ultrasonic cutting can cut any shape according to design requirements, with high cutting accuracy, which can effectively reduce material waste. Meanwhile, the heat generated during the cutting process is minimal and will not cause deformation of the plastic sheet.
Plastic component processing: In the production of plastic components, ultrasonic cutting can be used to cut complex shaped plastic parts, such as automotive interior parts, electronic and electrical casings, for edge material removal, hole processing, etc., which can improve the processing accuracy and surface quality of the parts and reduce subsequent processing costs.
Textile and clothing industry
Fabric cutting: It can accurately cut various textile fabrics, whether it is light and thin silk fabrics or thick denim fabrics, it can achieve smooth cuts without the occurrence of fabric edge shedding, fuzzing and other phenomena. Moreover, ultrasonic cutting can cut any shape according to the design pattern, meeting the personalized needs in clothing production.
Clothing accessory cutting: For various accessories on clothing, such as lining, lace, trademarks, etc., ultrasonic cutting can quickly and accurately cut them into the required size and shape, improving the processing efficiency and quality of accessories. At the same time, the high temperature generated during the cutting process can also heat melt the incision to prevent the edges from spreading apart.
Medical industry
Medical material cutting: In the processing of medical plastic pipes and sheets, ultrasonic cutting can ensure cutting accuracy and quality, meeting the strict requirements of medical devices for material size and performance. For example, in the manufacturing of medical catheters, it is possible to accurately cut catheters of different lengths and diameters, with smooth and burr free incisions, avoiding damage to human tissues.
Biological tissue cutting: In some surgical procedures, such as ophthalmic surgery, neurosurgery, etc., ultrasonic cutting technology can be used for precise cutting of biological tissue. It can reduce thermal and mechanical damage to surrounding tissues while cutting tissues, lower surgical risks, improve surgical success rates, and enhance patient rehabilitation outcomes.
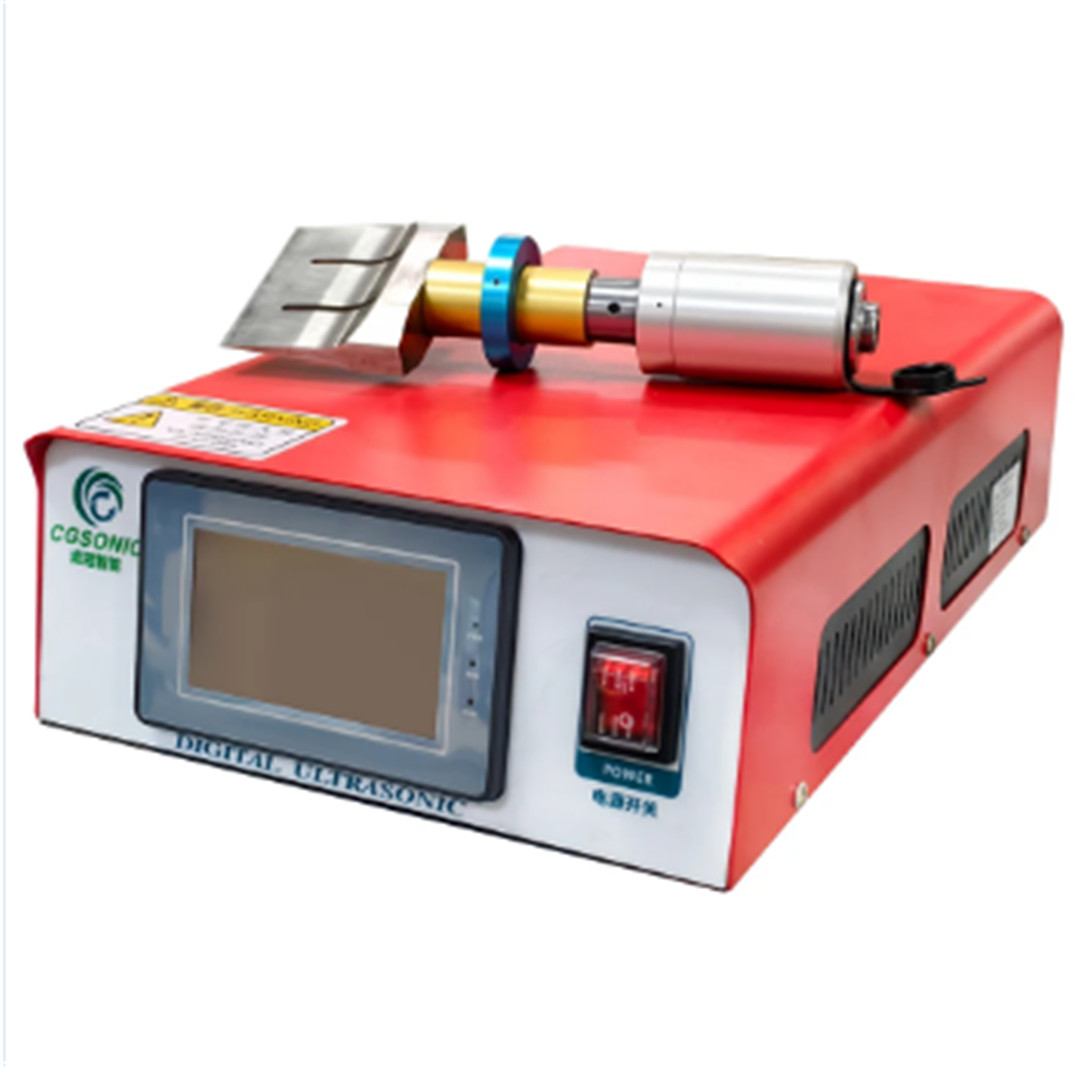
The water outlet machine is mainly used in the following fields:
Injection molding and mold making industry: This is one of the main application areas of waterjet machines. In the injection molding process, the product will have water nozzle materials. The water nozzle machine can cut and crush these water nozzle materials, and after screening, cleaning and other processes, ultimately produce reusable raw materials, achieving resource recycling and reducing production costs. At the same time, equipment such as ultrasonic nozzle vibration machines can also be used to directly vibrate the nozzle of injection molded plastic workpieces, suitable for PMMA PPE、PPS、PS、PC、PP、ABS、 Nylon and other hard thermoplastic products have smooth and non-destructive cutting edges, high efficiency, and save time and human resources.
Rubber industry: The water nozzle machine can treat the water nozzle of rubber products. In the production process of rubber products, such as rubber tires, rubber seals, etc., there will be excess water outlets after molding. The water outlet machine can remove them to meet the specified size and appearance requirements of the product, and the water outlet material can be recycled and reused to improve the utilization rate of rubber materials.
Plastic processing industry: In addition to injection molded plastic products, for products produced by other plastic processing techniques, such as extruded plastic pipes, plastic sheets, etc., a water nozzle machine can be used to cut the water nozzle of the pipe or trim the edges of the sheet to ensure the dimensional accuracy and appearance quality of the product. In addition, it can also be used to process various waste plastics and rubber products, such as waste car tires, waste household appliance shells, etc., with broad application prospects.
Metal die-casting industry: In recent years, products in the zinc alloy die-casting or aluminum alloy die-casting industries have increasingly used ultrasonic high-frequency vibration energy to remove water nozzles. By using an ultrasonic nozzle machine, the high-frequency vibration of ultrasonic waves can separate the nozzle of die-casting products, which is suitable for various decorative zinc die-casting products, such as furniture accessories, building decorations, bathroom accessories, automotive parts, lighting parts, toys, tie clips, belt buckles, various metal decorative buckles and other zinc alloy products. Compared with traditional cutting or polishing methods, it has higher efficiency, smoother cutting edges, and can reduce safety hazards of manual operation.
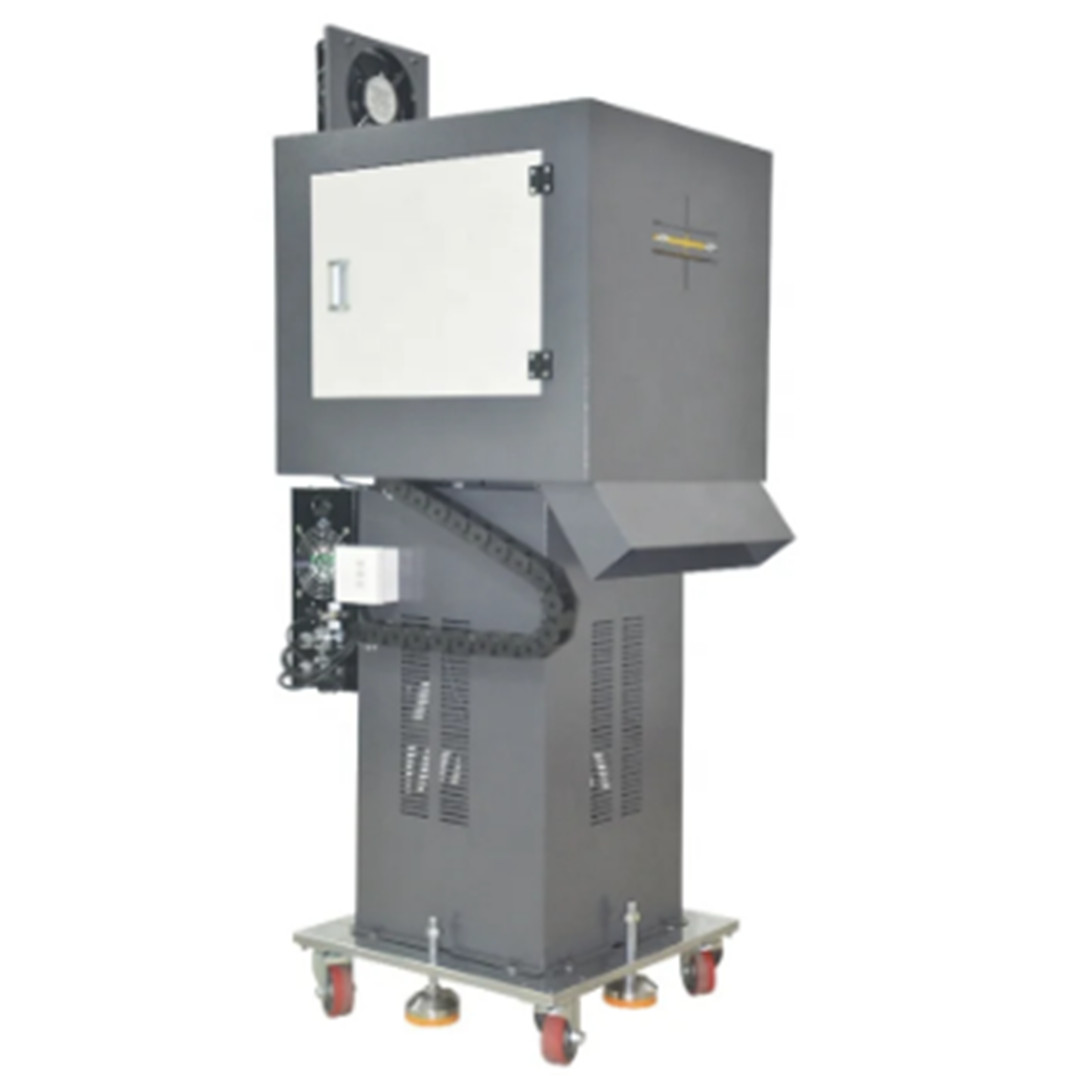
A homogenizer is a device used to refine and uniformly disperse particles or droplets in a liquid, and is widely used in multiple fields. The following are some of the main application areas:
The food and beverage industry can
Dairy products: used for the production of milk, yogurt, dairy beverages, etc. The fat globules in milk can be broken and evenly dispersed in lotion to prevent fat from floating, improve the stability and taste of the product, and make the texture of dairy products more delicate and even.
Beverage: In the production of fruit juice, tea drinks, functional drinks, etc., the homogenizer can refine and evenly distribute the fruit pulp particles in the fruit juice, prevent sedimentation and layering, improve the appearance and taste of the beverage, and evenly disperse the added nutrients such as vitamins, minerals, etc., ensuring the consistency of product quality.
Sauce: For sauce products such as jam, salad dressing, peanut butter, etc., the homogenizer can break down the particles in the raw materials and mix them thoroughly, making the texture of the sauce more delicate, smooth, and with a better taste, while extending the shelf life of the product.
cosmetics industry
Lotion face cream: In the production of skin care products such as lotion, face cream and essence, the homogenizer evenly mixes oil, wax, water and various functional ingredients, so that the product has fine texture and good stability, and is easy to apply and absorb.
Makeup: used for the manufacture of lipstick, eye shadow, foundation make-up and other cosmetics products. It can evenly mix pigments, oils, waxes, and other ingredients to ensure uniform and delicate product color, improving product quality and effectiveness.
Pharmaceutical industry
Emulsion: In the production of emulsion based drugs, such as fat emulsion injections, oral emulsions, etc., homogenizers can evenly mix the oil and water phases in the drug to form stable emulsions, improving the stability and bioavailability of the drug.
Suspension agent: For suspension drugs such as suspensions, suspension tablets, etc., homogenizers can refine and evenly disperse drug particles in the medium, prevent particle settling, and ensure the accuracy and uniformity of drug dosage.
Chemical industry
Coatings: In the production of coatings, homogenizers can evenly disperse solid particles such as pigments and fillers in resin and other base materials, improve the covering power, color uniformity, and stability of coatings, prevent pigment precipitation, and improve the construction performance and coating quality of coatings.
Ink: Used in the production process of ink, it can fully mix and disperse the pigments, binders, and other components in the ink, ensuring bright and uniform colors, good transfer performance during printing, and improving printing quality.
Glue: In the production of glue and adhesives, homogenizers help to evenly mix various high molecular weight polymers, fillers, plasticizers, and other components, making the glue have good viscosity, stability, and fluidity, meeting the needs of different application scenarios.
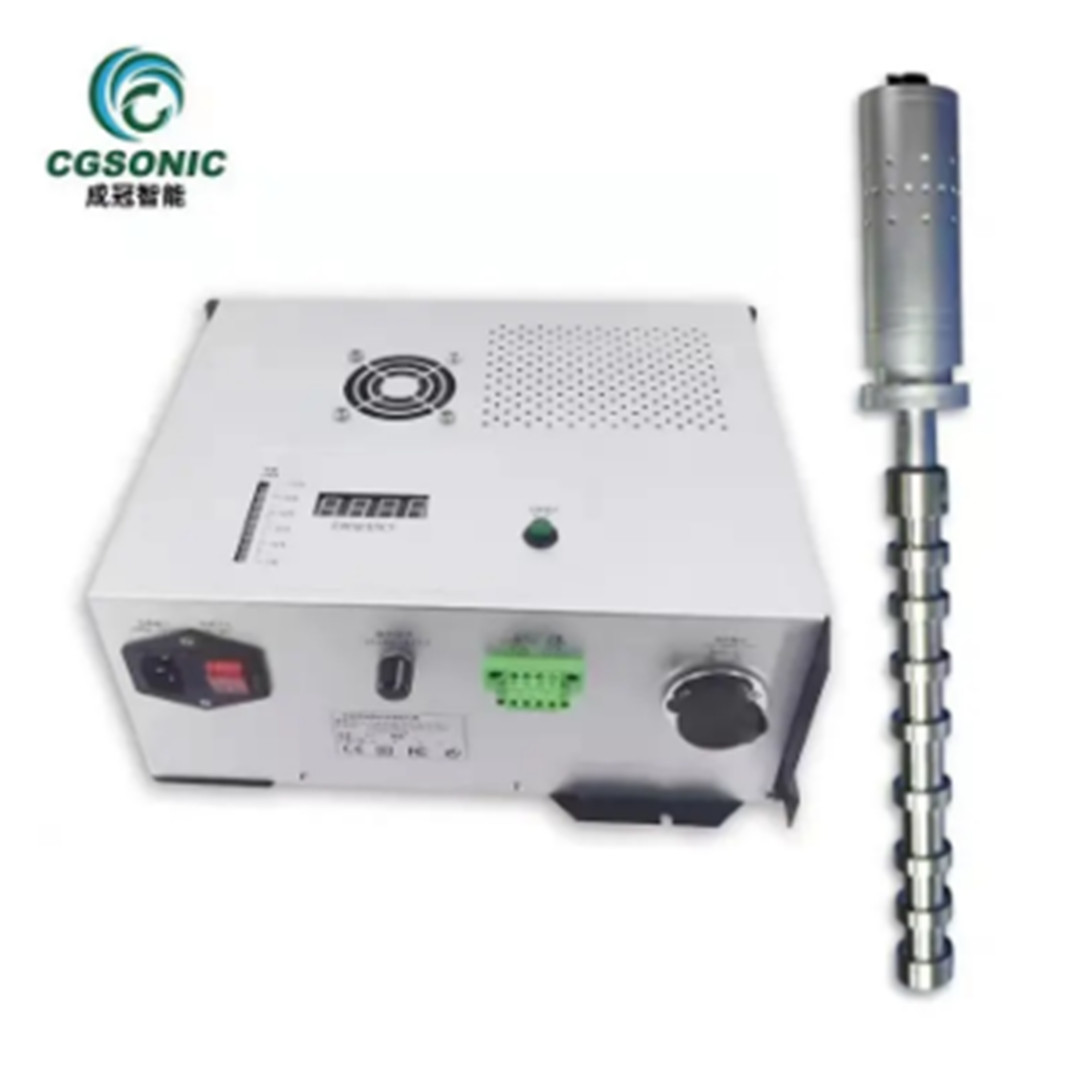