01
Ultrasonic automation system
Working Principle
The automation control system controls the ultrasonic generator to generate high-frequency electrical signals of specific frequency and power according to a preset program. The signal is transmitted to the transducer, converted into mechanical vibration of the same frequency, amplified by the amplitude rod, and applied to the processing object. During the processing, sensors continuously collect data and provide feedback to the automation control system. The system adjusts various parameters in real time based on the feedback information to ensure the accuracy and stability of the processing.
Product Introduction
Composed of ultrasonic generator, transducer, ultrasonic mold and other parts. The ultrasonic generator is responsible for generating high-frequency electrical signals; The transducer converts electrical signals into mechanical vibrations; The automation control system issues operational instructions and coordinates the work of various components; Mechanical transmission devices achieve precise position movement and action execution; Sensors monitor various parameters during the processing in real-time, such as pressure, temperature, displacement, etc.
application area
Electronics industry: used for soldering and assembling precision electronic components such as chips and circuit boards, ensuring precise connection of small components and meeting the requirements of miniaturization and high precision of electronic products.
Automobile manufacturing: realizing the welding of plastic parts for automobile interiors, sensor packaging, and other work, improving production efficiency, ensuring component connection strength, and adapting to large-scale automobile production.
Medical equipment: Welding and assembly of medical consumables such as assistive catheters and infusion sets to ensure product sterility, sealing, and compliance with strict medical standards.
Packaging field: Complete the sealing and welding of packaging containers for food, medicine, cosmetics, etc., ensure packaging sealing, extend product shelf life, and adapt to high-speed packaging production lines.
Daily necessities production: In the production of plastic toys, stationery, household items, etc., plastic parts are welded and assembled to improve production efficiency and product quality.
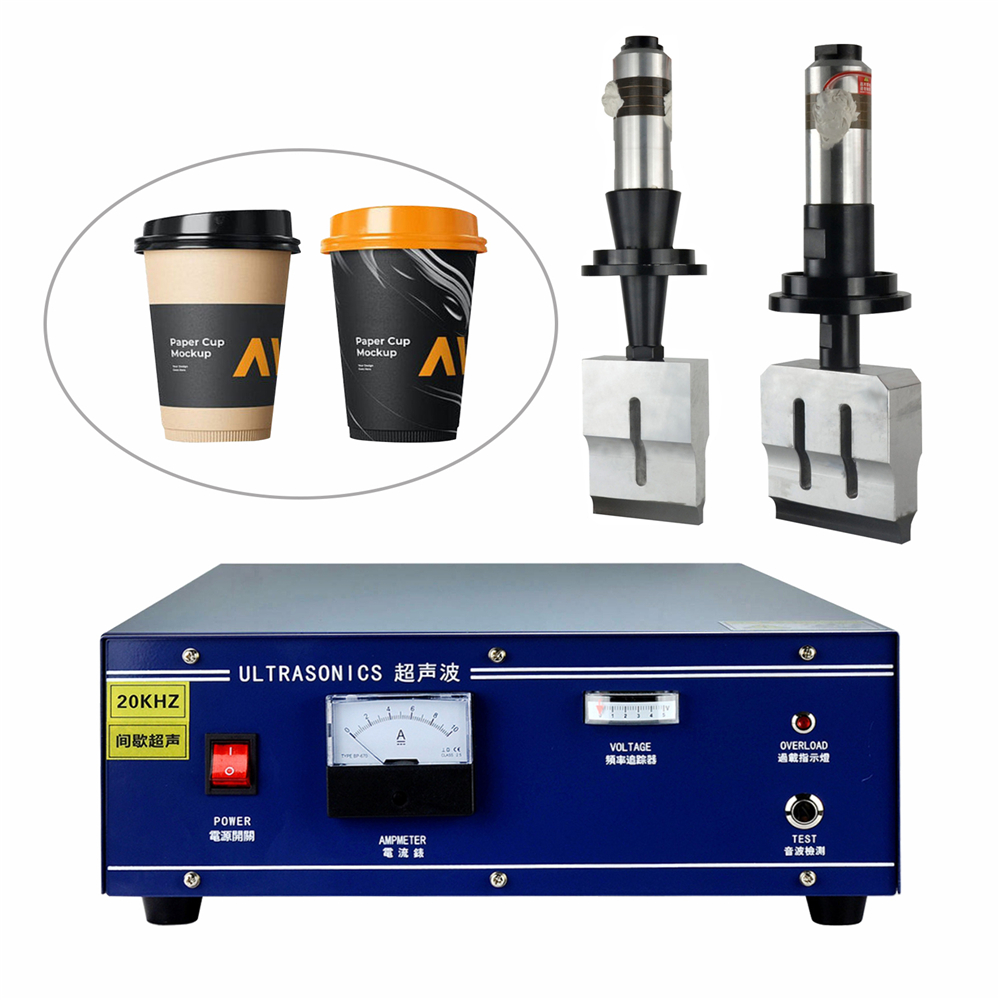
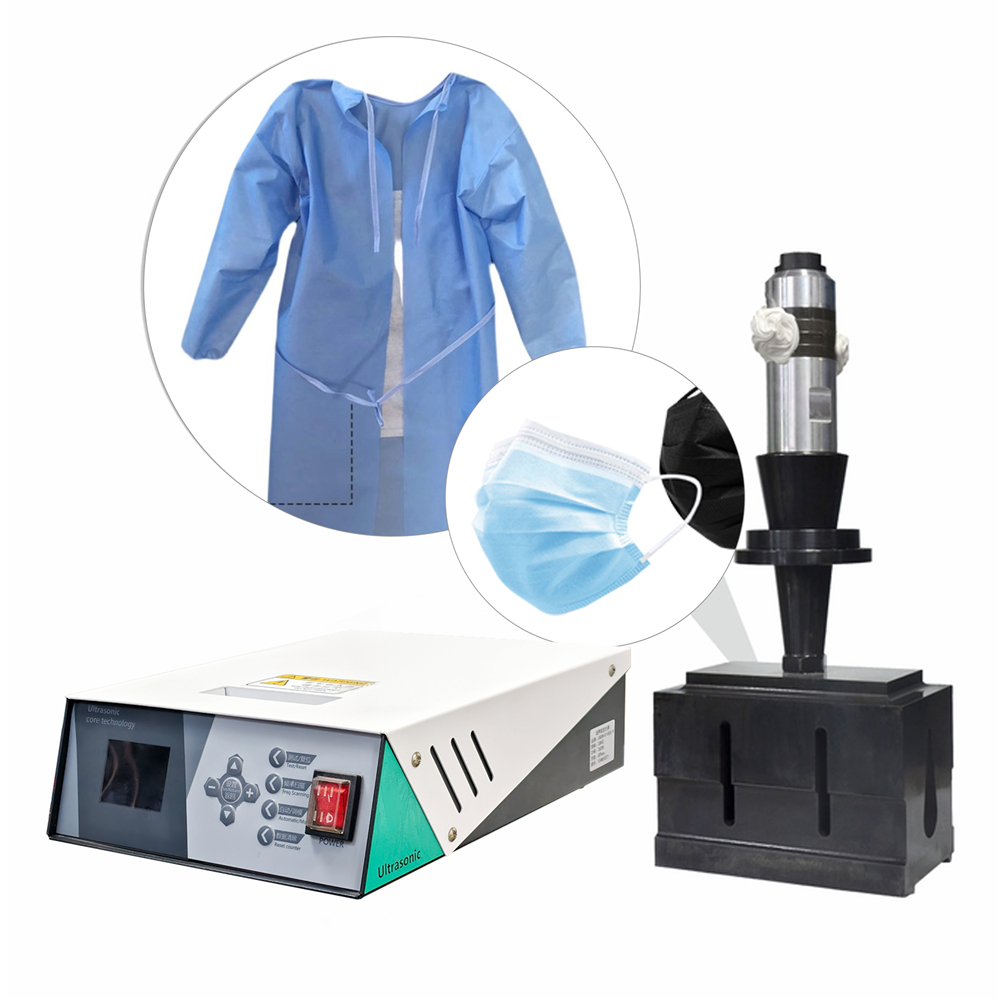
Detail Display
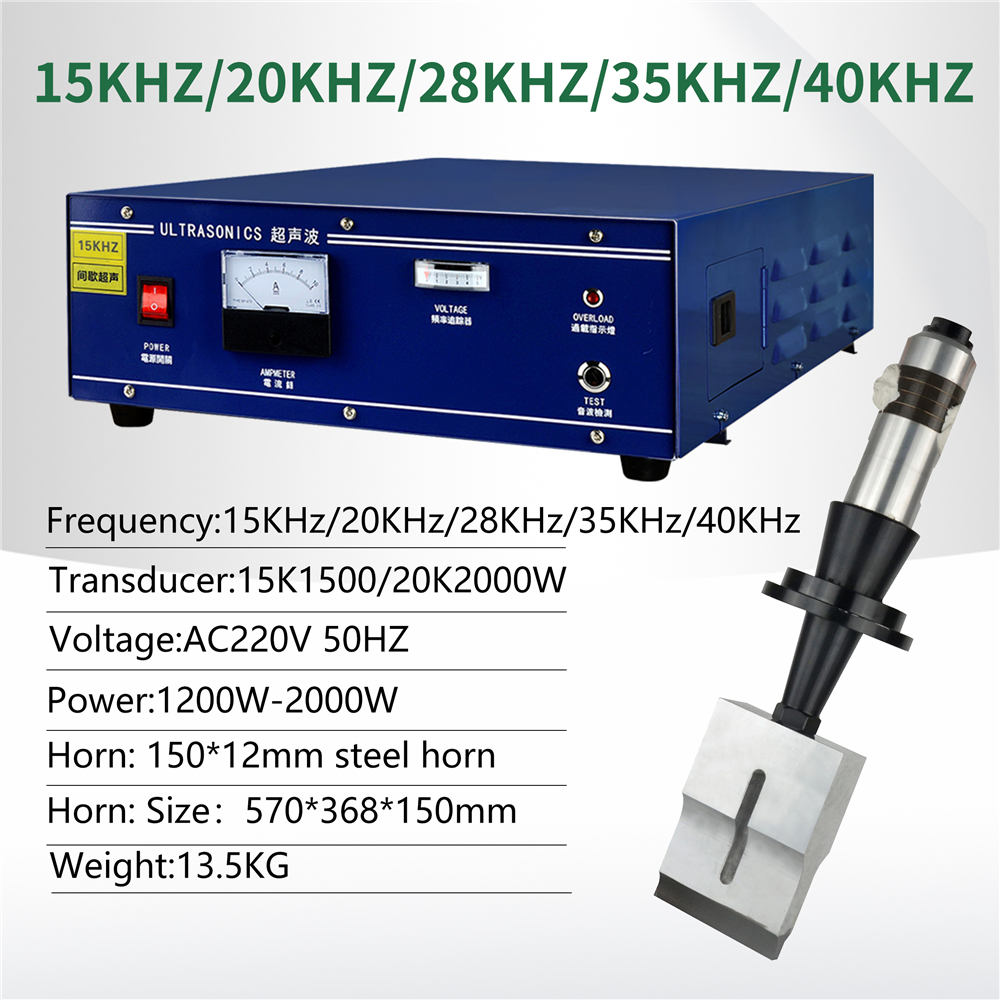
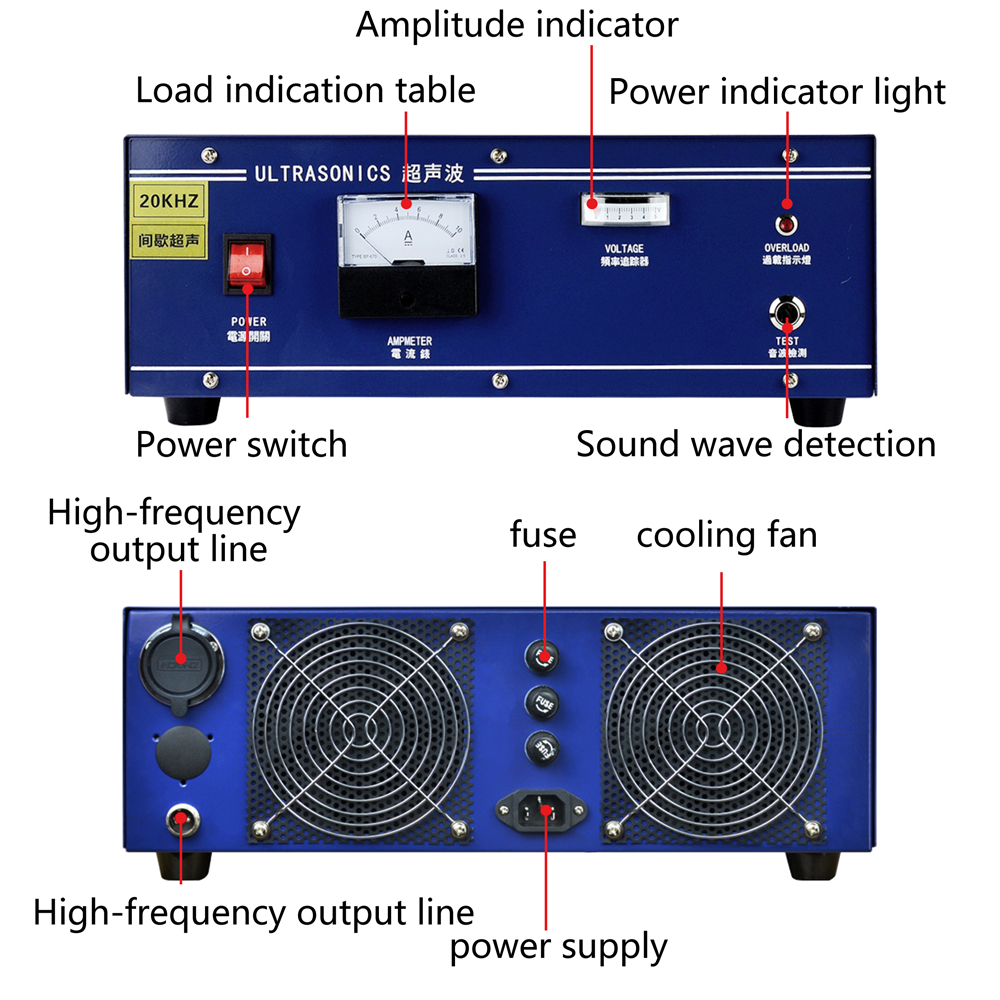
Mold customization
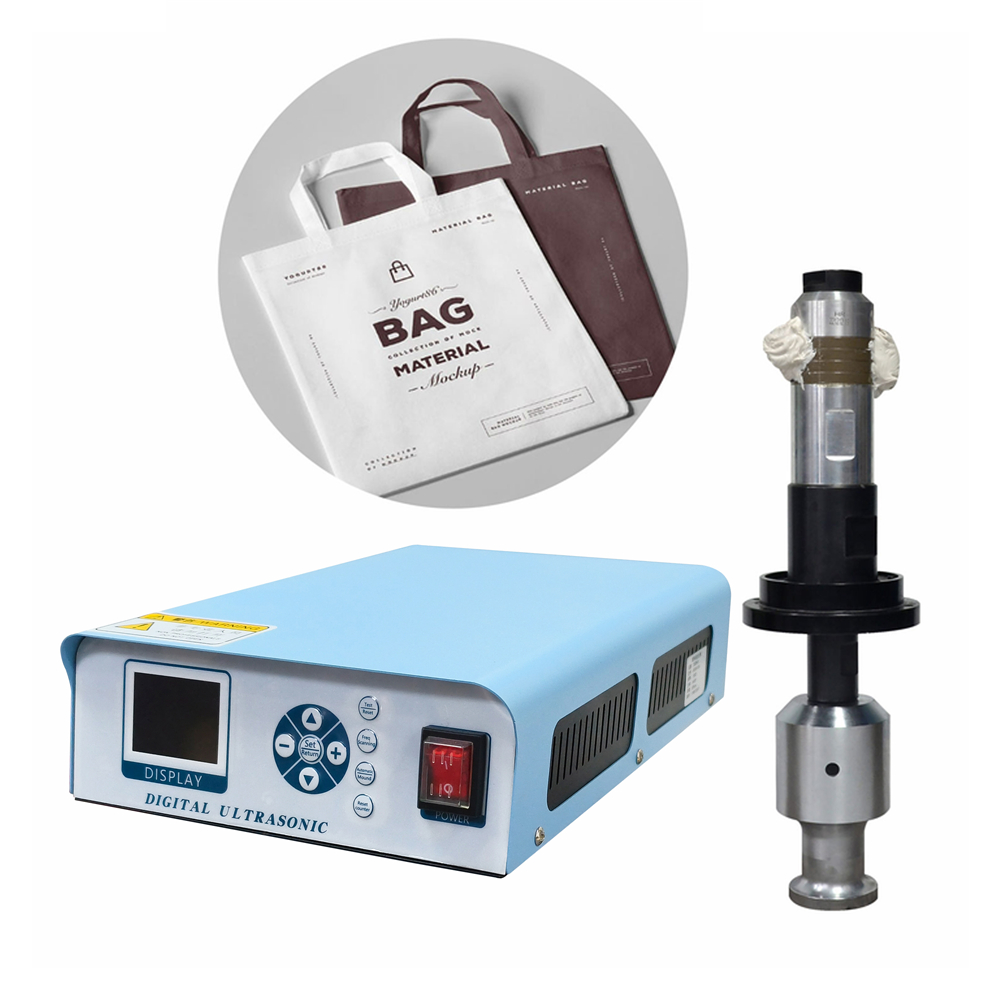
Operating Frequency |
15KHz/20KHz/28KHz/35KHz/40KHz |
Output Power |
600~3500W |
Input Voltage |
AC220v 50Hz |
Amplitude Adjustment |
1%~100% |
Weld Time |
0.01~9.99s |
Machine maintenance and upkeep
Ultrasonic generator: Regularly check the circuit connections of the generator to ensure no looseness or damage, and avoid short circuits or open circuit faults. Keep the working environment of the generator dry and ventilated, prevent overheating, regularly clean the internal dust, and maintain stable power output and frequency accuracy.
Transducers and amplitude rods: Check if the connection between the transducers and amplitude rods is secure, and if there are any cracks, wear, or other abnormalities. If there is a problem, replace it in a timely manner. Avoid external impact and ensure effective conversion and transmission of ultrasonic energy.
Mechanical transmission components: Regularly add suitable lubricating oil to transmission components such as motors, screws, slides, chains, etc. to reduce wear and ensure smooth transmission. Check the tension of the belt to prevent slipping, and replace severely worn belts in a timely manner. At the same time, tighten the bolts at each mechanical connection to prevent loosening.
Control system: Check whether the control buttons, touch screen, etc. respond normally, and promptly repair or replace damaged parts. Regularly backup system data to prevent data loss, update control programs, and optimize device performance.
Sensors: Regularly calibrate various sensors, such as position sensors, pressure sensors, etc., to ensure their detection accuracy. Clean the dust and debris on the surface of the sensor to avoid affecting the detection effect.
Regular testing: Conduct comprehensive testing of the entire system on a regular basis, including ultrasonic output intensity, mechanical motion accuracy, automation control processes, etc., to promptly identify and solve potential problems.
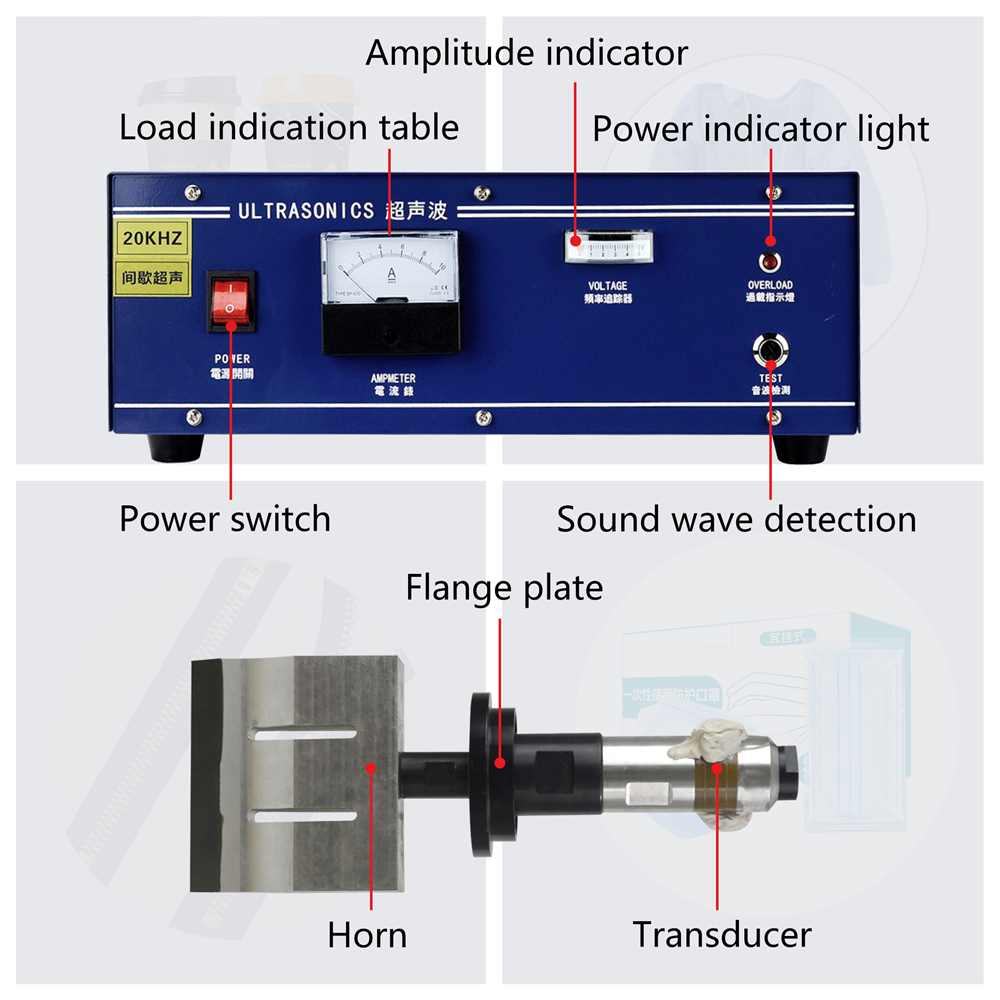
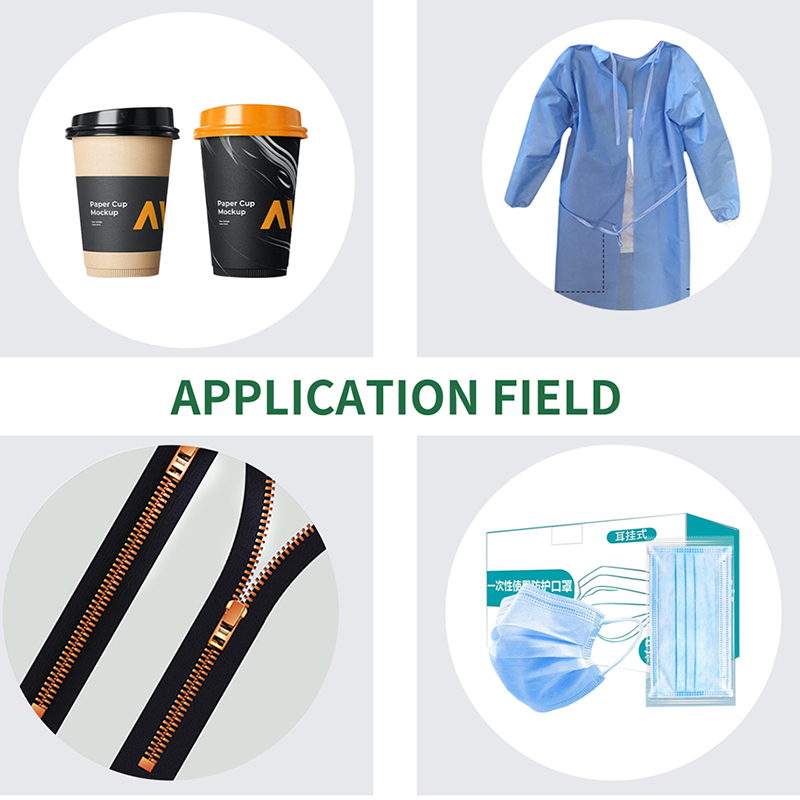