01
Ultrasonic food cutting machine
short description part
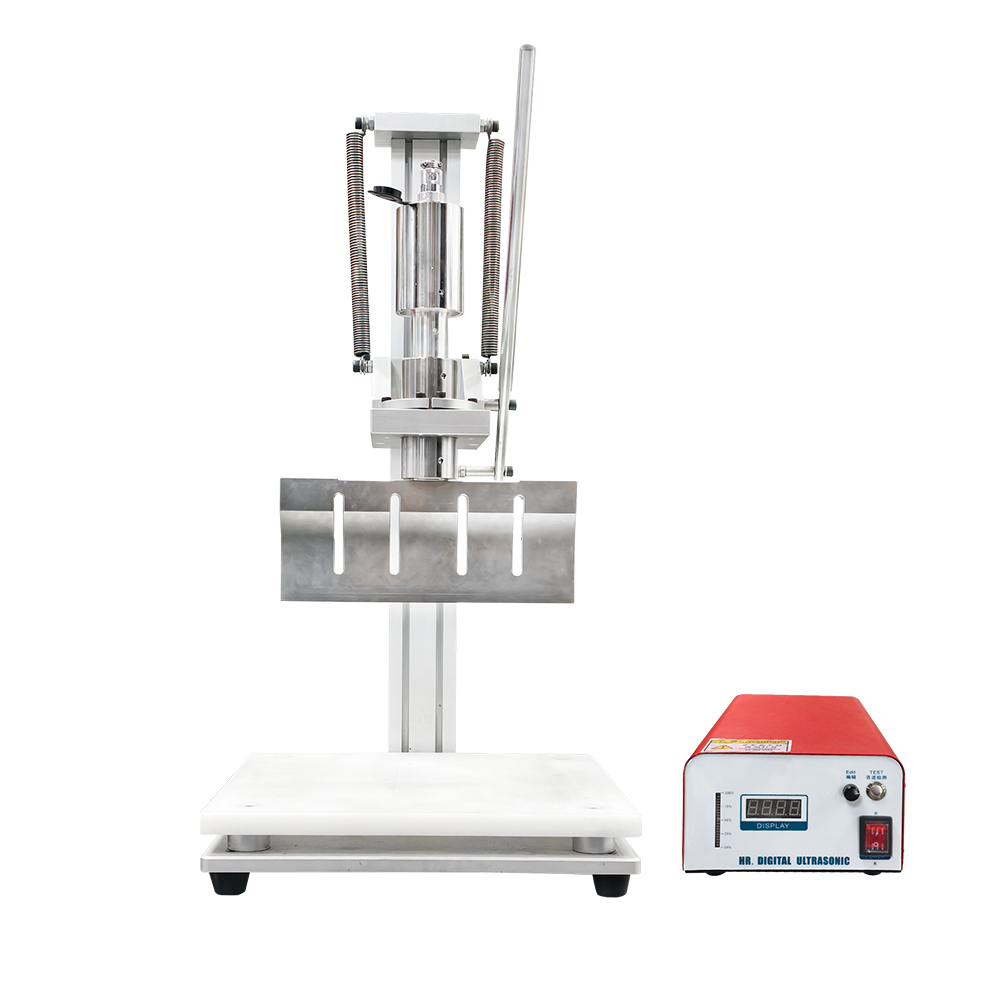
Reduce food loss : During the cutting process, the knife contacts the food instantly and the friction is small, which reduces the damage and deformation of food caused by friction and reduces the scrap rate. When cutting toast, it can prevent the bread slices from breaking due to friction and keep them intact.
Heat-free cutting ensures quality : The cutting process generates almost no heat, avoiding the impact of high temperature on the taste, nutritional value and appearance of food, and maintaining the original texture and flavor of food. For example, when cutting temperature-sensitive foods such as chocolate, it can prevent them from melting and deforming.
Hygienic, safe and reliable : Reduce contact contamination during the cutting process, no need to use chemical substances such as tool lubricants, ensure food hygiene and safety, and meet the strict hygiene standards of the food processing industry.
working principles
Ultrasonic food cutting machines operate on the principle of high-frequency vibration. The ultrasonic generator in the equipment produces high-frequency electrical signals, which are converted into high-frequency mechanical vibrations by the transducer and transmitted to the cutting head. When cutting, the high-frequency vibration of the cutting head acts on the surface of the food, generating local high-frequency friction heat, allowing the food to be cut with minimal heat. The entire process does not require a sharp blade or excessive pressure to complete the cutting action.
Product Introduction
Ultrasonic food cutting machine uses ultrasonic generator to generate high-frequency electrical signal, which is converted into high-frequency mechanical vibration by transducer to act on the cutting head to achieve food cutting. It has high efficiency, precision and uniformity in cutting, can reduce food loss, and adopts heatless cutting to maintain food quality and hygiene and safety. It is widely used in baking, frozen food, meat, fruit and vegetable processing and other industries to meet the cutting needs of different foods.
application areas
Baking industry: used to cut bread, cakes, pizza and other baked goods. It can be cut accurately according to the shape and size requirements of different products to improve the appearance of the products.
Frozen food processing: cutting frozen foods such as ice cream, frozen dough, quick-frozen dumplings, etc. Due to its non-heat cutting characteristics, it can prevent frozen foods from melting and deforming, ensuring product quality.
Meat processing: Cutting sausages, hams and other meat products can achieve precise cutting while avoiding excessive damage to meat fibers and retaining the taste and nutrition of the meat.
Fruit and vegetable processing: For softer fruits and vegetables, such as strawberries and tomatoes, fine cutting can be achieved to reduce juice loss and pulp damage.
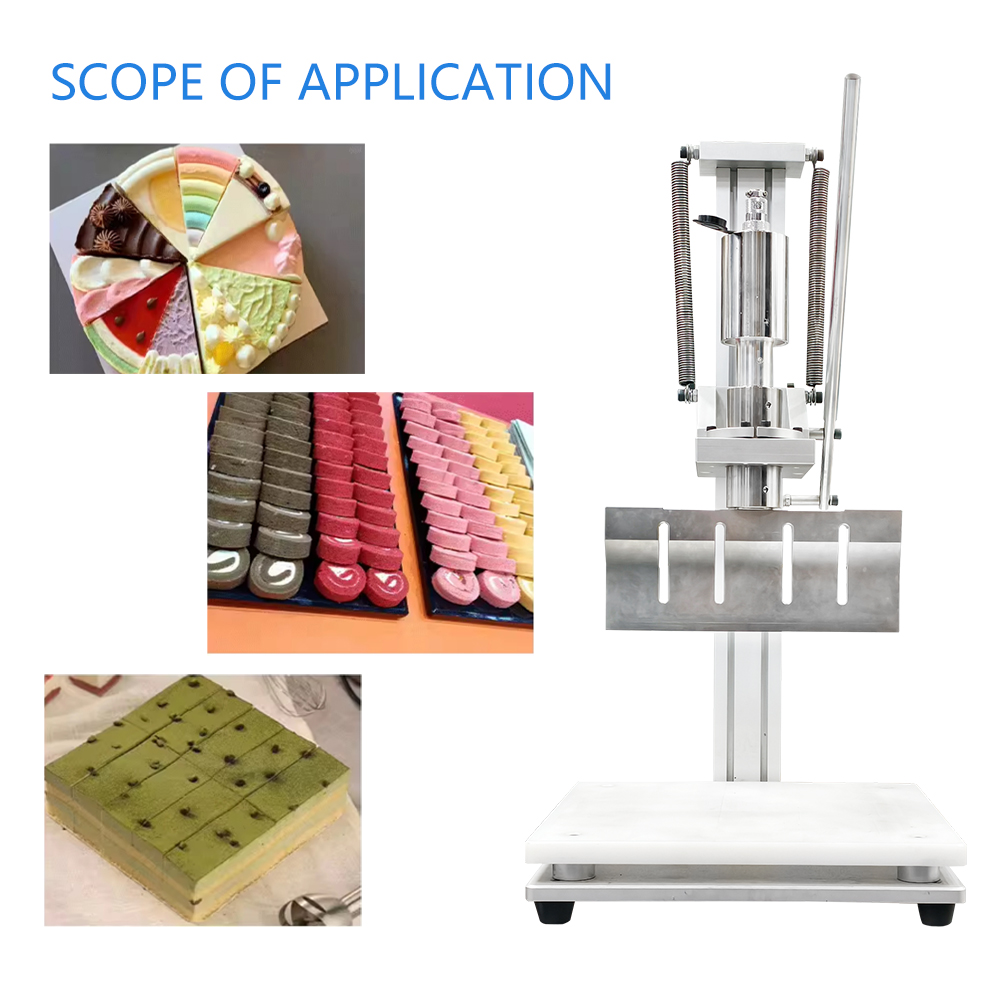
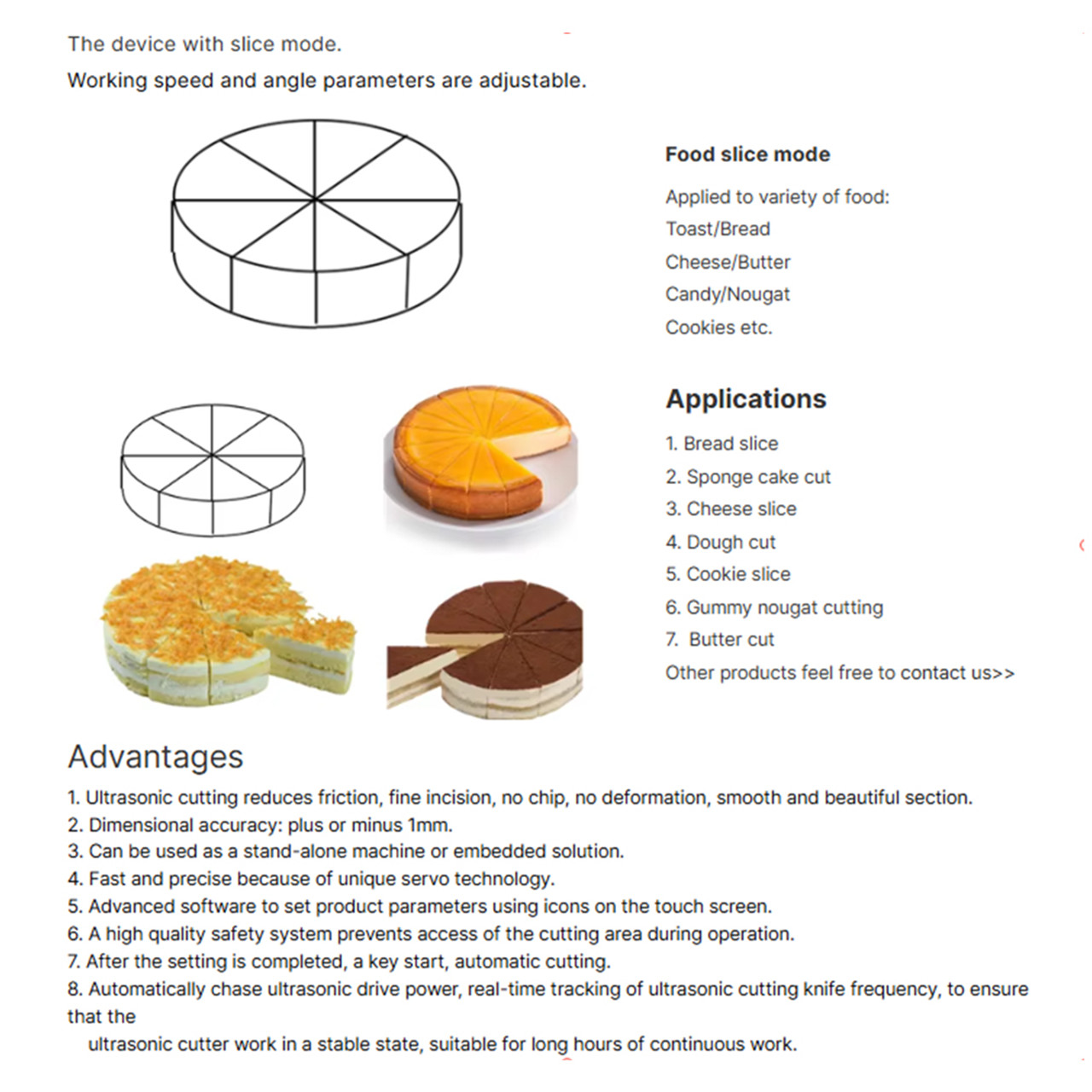
details display
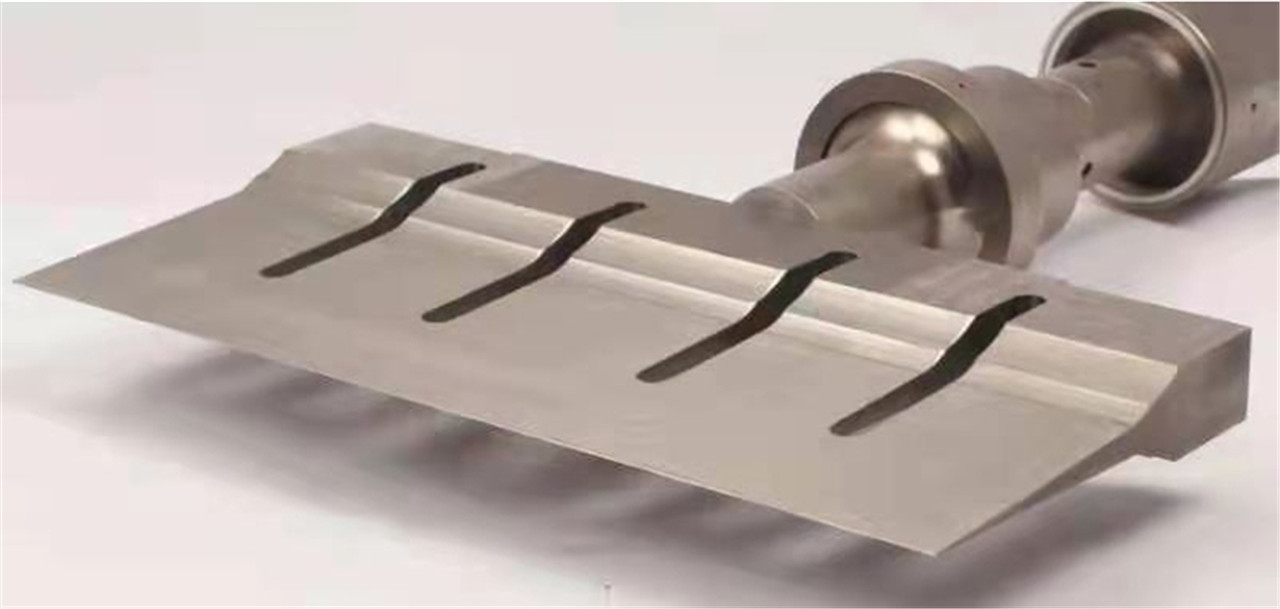
Product Parameters
Operating frequency |
15KHz/20KHz/28KHz |
Output Power |
1500~3000W |
Input voltage |
AC220v 50Hz |
Amplitude adjustment |
1%~100% |
Welding time |
0.01~9.99s |
Machine size |
290*380*110mm |
Machine weight |
16kg |
Access air pressure |
0.1~0.7MPa |
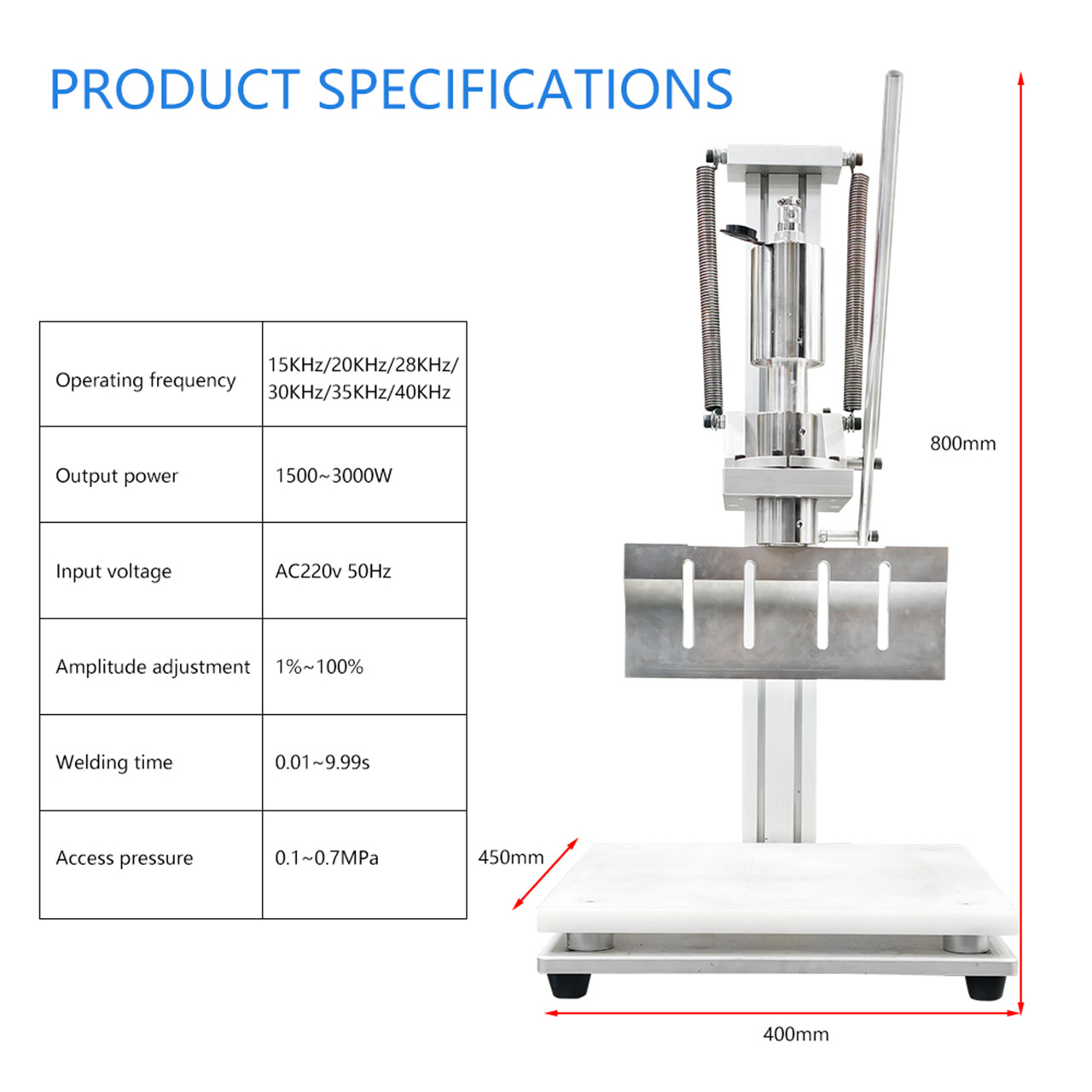
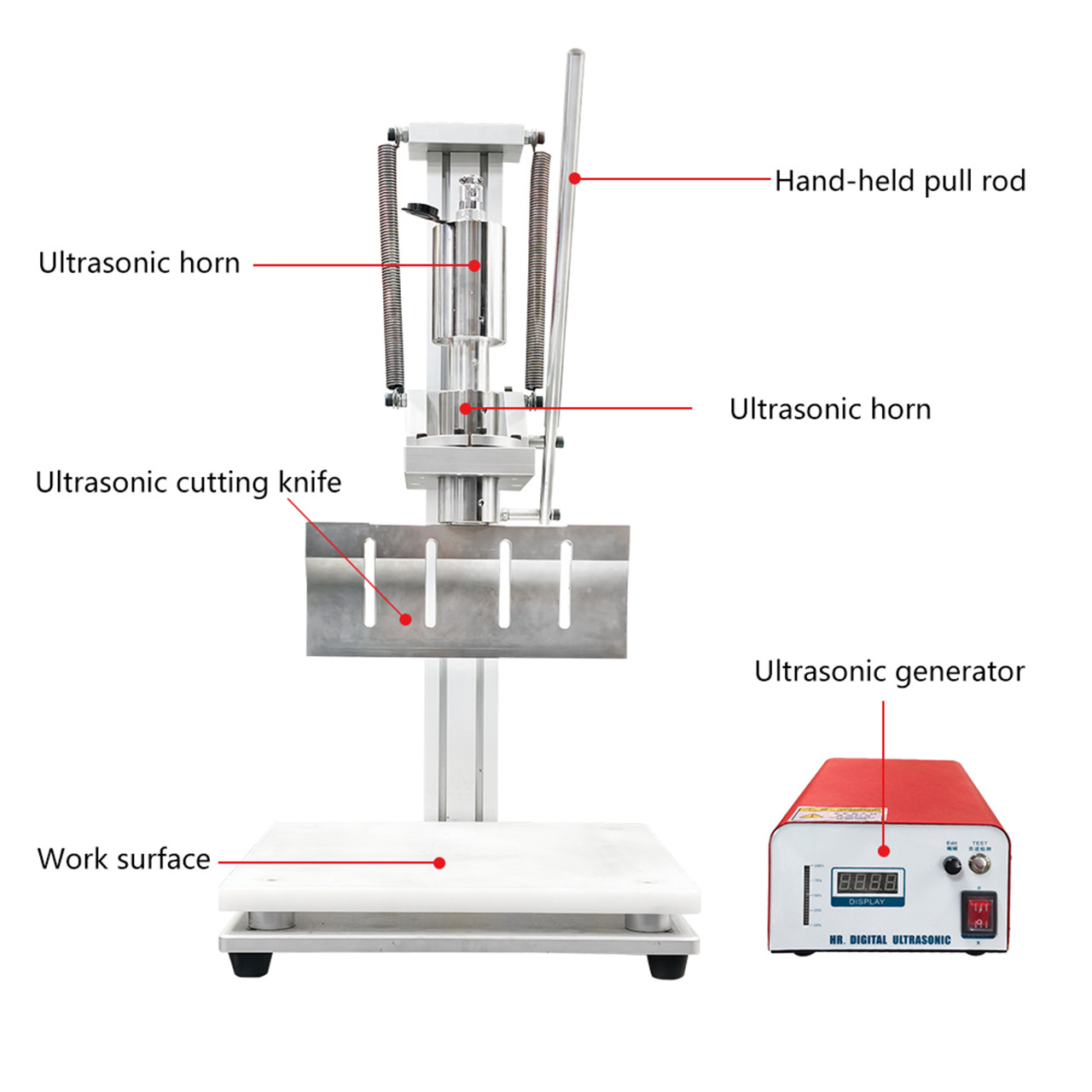
Machine maintenance
Cutting tools: After each use, clean the blade of the knife promptly to prevent corrosion and blockage. Check the wear of the knife regularly. If the blade becomes blunt or has a chip, replace it in time to ensure cutting accuracy.
Ultrasonic system: Keep the ultrasonic generator dry and ventilated, clean dust regularly, and avoid overheating or moisture. Check the generator parameters to ensure stable output power and frequency. Check whether the transducer and horn are firmly connected and whether there is any damage. If there is any problem, deal with it in time.
Mechanical parts: Regularly add lubricating oil to transmission parts such as motors, chains, guide rails, etc. to reduce wear and ensure smooth operation. Check the screws of each connection and tighten the loose parts in time.
Electrical system: Check whether the circuit is damaged or aged to prevent short circuit and leakage. Clean the dust of electrical components regularly to ensure good heat dissipation. Test whether the control buttons and display screen are working properly. If there is any fault, repair or replace it in time.
Machine inspection: Regularly conduct comprehensive performance inspections on the equipment, such as cutting speed, cutting effect, ultrasonic output intensity, etc., to promptly discover and solve potential problems and ensure stable operation of the equipment.
After-Sales Service
We provide a one-year warranty service for our products and will fully protect your usage rights during the warranty period. In addition, if you encounter any questions or technical issues during use, our professional online technical support team will be available to answer your questions and provide you with efficient and thoughtful solutions.
Ultrasonic Plastic Welding Machines | CE-Certified for Global Quality
✅ CE Certified Excellence:All our ultrasonic welding equipment is CE-certified, meeting strict EU safety & quality standards. Rigorous testing ensures reliable performance for global applications.
✅ High-Efficiency :Welding SolutionsUltra-high frequency technology ensures firm, bubble-free joints for auto parts, electronics, medical devices, etc.Intelligent control system allows precise parameter adjustment, boosting production efficiency by 30%+.
✅ Direct from Manufacturer:20+ years of expertise in custom solutions. Factory-direct pricing + comprehensive after-sales support—your one-stop welding partner.
📞 Contact us today for CE-certified machines and tailor-made welding solutions! Elevate your production with certified quality.