01
Ultrasonic multi-frequency transducer
working principles
Ultrasonic transducer is a device that can convert electrical energy and mechanical energy into each other. Its working principle is mainly based on piezoelectric effect and inverse piezoelectric effect.
Piezoelectric effect : Certain crystal materials, such as quartz and piezoelectric ceramics, will generate electric charges on their surfaces when subjected to external forces. This phenomenon of converting mechanical energy into electrical energy is called the piezoelectric effect. When an ultrasonic transducer is used as a receiver, it works using the piezoelectric effect. When ultrasonic waves propagate in a medium, they will cause the piezoelectric material of the transducer to generate mechanical vibrations, which in turn generate electric charges on the surface of the piezoelectric material. The electrical signals formed by these charges can be detected after being amplified and processed, thereby realizing the function of converting ultrasonic signals into electrical signals.
Inverse piezoelectric effect : When an electric field is applied to a piezoelectric material, the piezoelectric material will produce mechanical deformation. This phenomenon of converting electrical energy into mechanical energy is called the inverse piezoelectric effect. When an ultrasonic transducer is used as a transmitter, the inverse piezoelectric effect is used. When an alternating electric field is applied to the piezoelectric material of the transducer, the piezoelectric material will produce periodic mechanical vibrations under the action of the electric field. This vibration propagates in the medium to form ultrasonic waves, thereby realizing the function of converting electrical signals into ultrasonic signals.
Product Introduction
Transducer, also known as active sensor, is a key device that can realize the mutual conversion of different forms of energy such as electrical energy, mechanical energy or acoustic energy. It plays a core role in many devices that rely on energy conversion. For example, in ultrasonic equipment, the transducer is the core device that realizes the conversion of electrical energy and acoustic energy.
There are many types of transducers. According to the physical properties and materials used, the most common ones are magnetostrictive transducers and electrostrictive transducers. From the perspective of working principle, they can be divided into mechanical, capacitive, piezoelectric, magnetostrictive, thermal resistor and other transducers. Different types of transducers differ in structure, performance and applicable scenarios. For example, piezoelectric transducers work by relying on the piezoelectric effect of piezoelectric materials and are widely used in sensors, vibrators, sound converters and other fiel.
The operating frequency, bandwidth, electroacoustic frequency, impedance at resonant frequency, directivity (transmitting beam width) and sensitivity are important indicators for measuring transducer performance. These indicators directly affect the performance of the transducer in practical applications. Taking the operating frequency as an example, different application scenarios have different requirements for it. The operating frequency of low-frequency transducers is lower than 100Hz, the medium frequency is between 100Hz and 1kHz, and the high frequency is higher than 1kHz.
application areas
Industrial field: In ultrasonic welding, plastic or metal materials are connected; it can also be used in ultrasonic processing to cut and drill brittle and hard materials. Ultrasonic cleaning, welding, cutting and other processes are all achieved with the help of transducers.
Medical field: such as ultrasonic diagnostic equipment, which transmits and receives ultrasonic waves through the transducer to form images of internal tissues of the human body for disease diagnosis; both ultrasonic diagnosis (such as B-ultrasound, color ultrasound) and ultrasonic treatment (such as ultrasonic scalpel, ultrasonic lithotripsy) are inseparable from it.
Life field: Commonly used in ultrasonic humidifiers, which atomize water into tiny particles to increase
Air humidity: there are also ultrasonic toothbrushes, which use ultrasonic vibrations to clean teeth.
Military field: Sonar systems use ultrasonic transducers to detect, locate and communicate underwater targets.
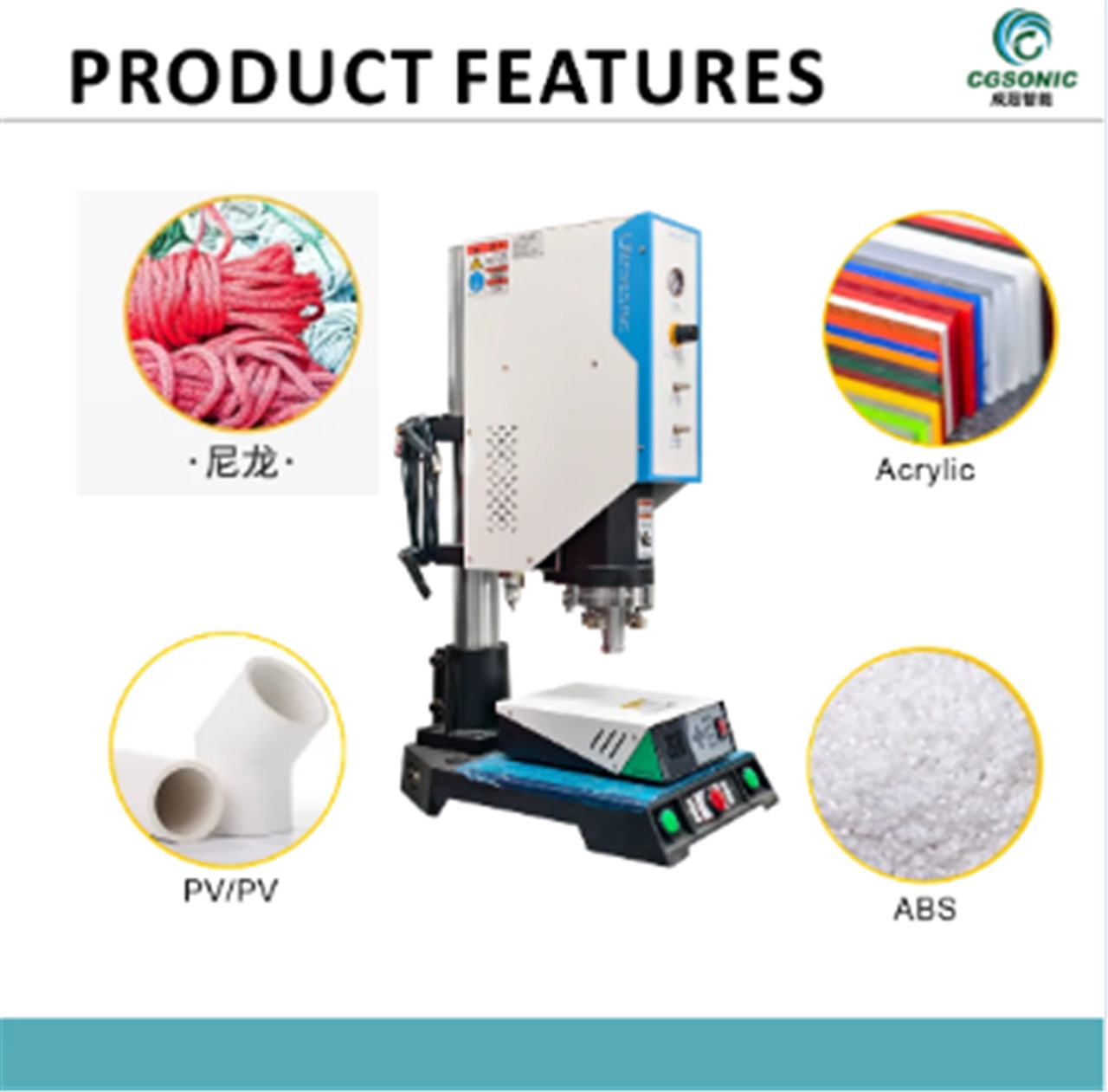
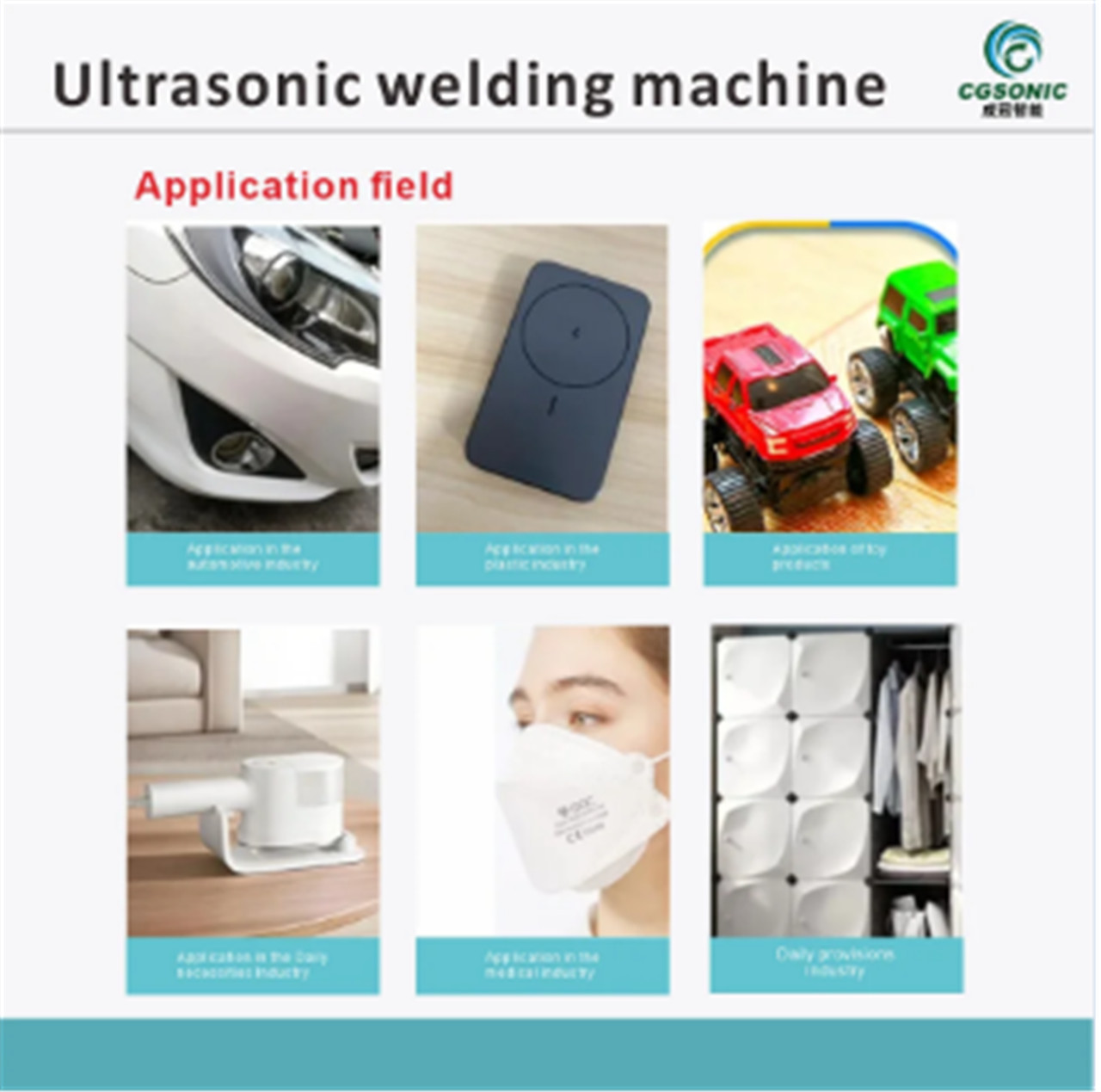
details display
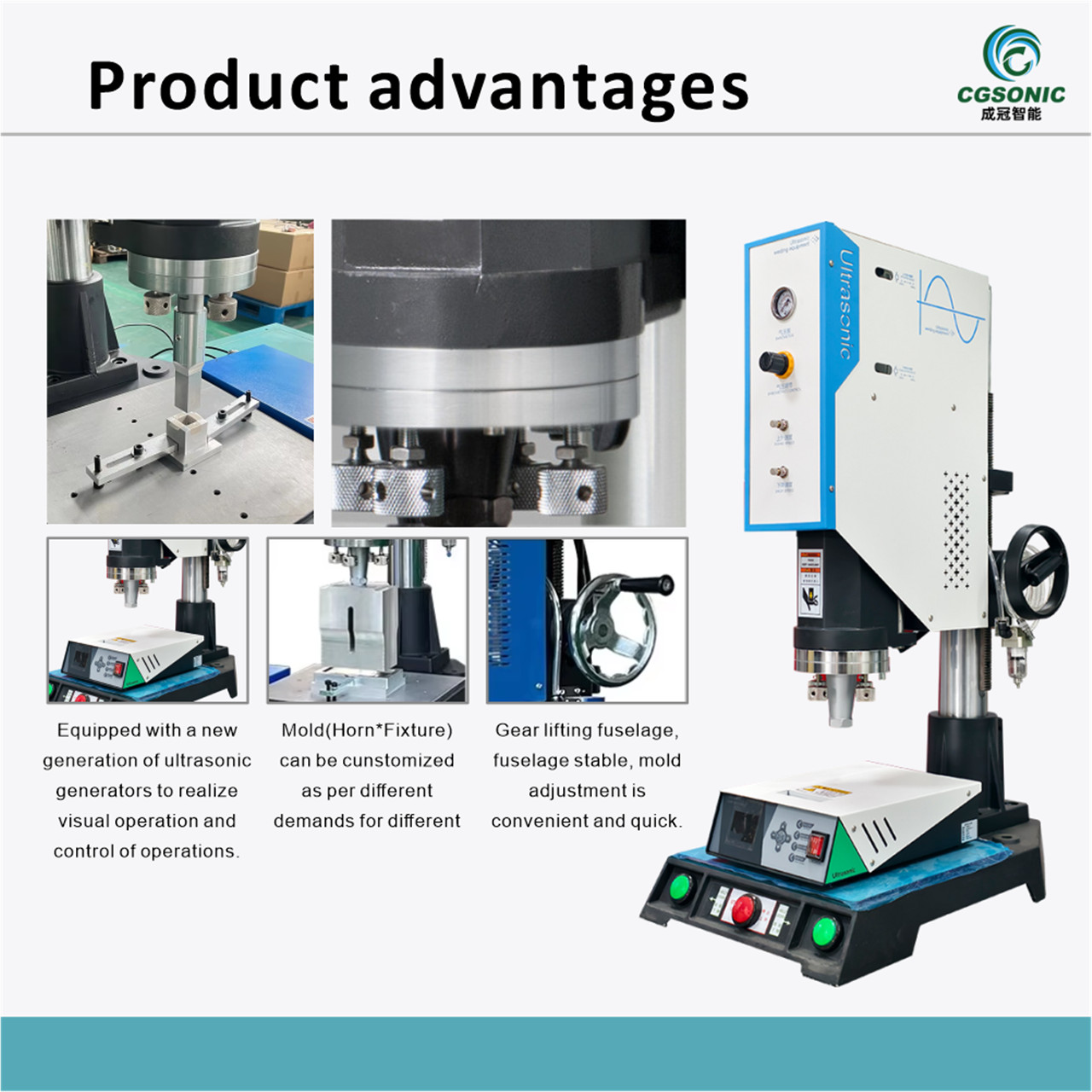
Product Parameters
Operating frequency |
15KHz20KHz/28KHz/35KHz/40KHz |
Output Power |
600~3500W |
Input voltage |
AC220v 50Hz |
Amplitude adjustment |
/ |
Welding time |
/ |
Product size |
custom made |
Machine weight |
custom made |
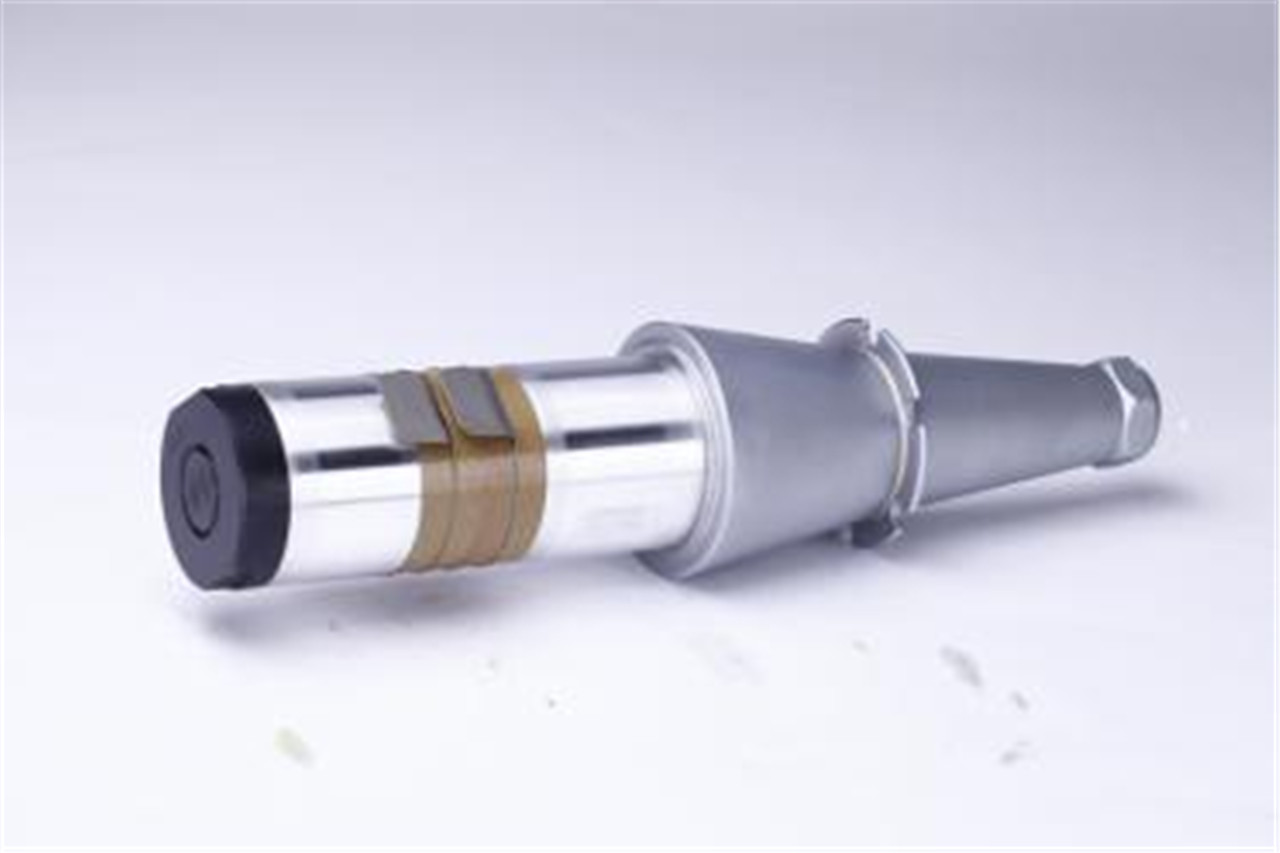
Machine maintenance
Cleaning and maintenance: Regularly wipe the surface of the transducer with a soft, dry cloth to remove dust, oil and other impurities to prevent pollutants from affecting its performance. Be careful not to use corrosive cleaning agents to avoid damaging the housing.
Performance testing: Regularly use professional instruments to test the electrical performance parameters of the transducer, such as impedance, capacitance, resonant frequency, etc., to ensure that they are within the normal range. Once a large deviation in the parameters is found, the cause of the fault needs to be investigated.
Installation and disassembly: During installation, ensure that the installation position is stable and avoid vibration and impact; connect the lines strictly in accordance with the operating procedures to prevent wrong or false connections. During disassembly, operate carefully and avoid violent pulling to avoid damaging the internal structure.
Storage requirements: If not used for a long time, the transducer should be stored in a dry, ventilated environment without corrosive gases to avoid moisture and oxidation to extend its service life.
After-Sales Service
Our products come with a one-year warranty service and fully protect your right of use during the warranty period. In addition, if you encounter any problems or technical issues during use, our professional online technical support team will be at your service to answer your questions and provide efficient and thoughtful solutions.